Self-powered sensors transform robotics technology
Discover how piezoelectric and triboelectric sensors are transforming industries with advanced tactile sensing and AI integration.
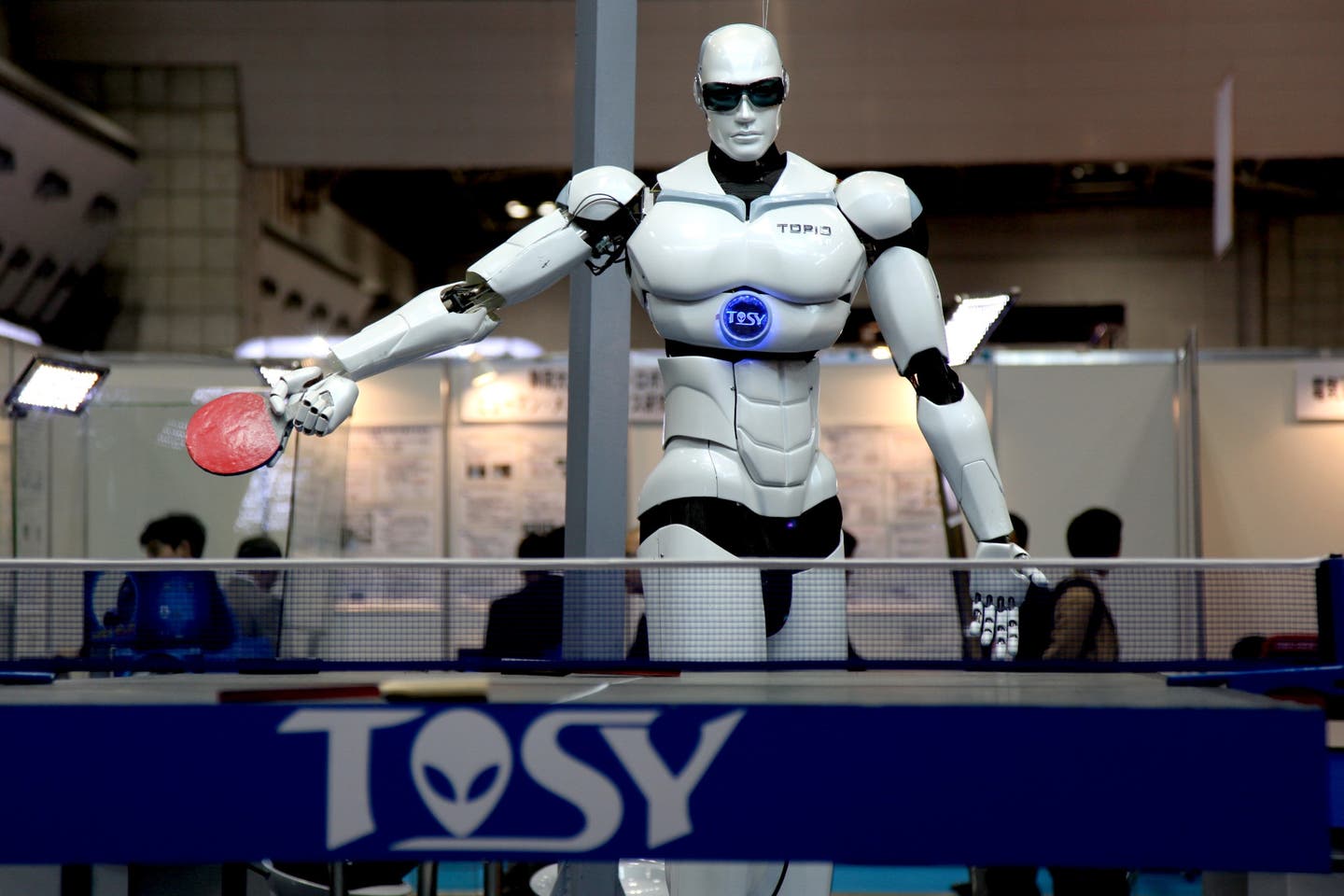
Piezoelectric and triboelectric sensors are redefining technology by enabling high-sensitivity tactile sensing for healthcare, robotics, and wearable devices. (CREDIT: Humanrobo)
The quest to mimic human touch in technology has led researchers to explore piezoelectric and triboelectric effects as pivotal phenomena. These effects underpin a new generation of tactile sensors designed for applications in robotics, wearable devices, and healthcare. By converting mechanical stimuli into electrical signals, these technologies promise unprecedented precision and adaptability.
The piezoelectric effect involves generating voltage through mechanical stress. This phenomenon occurs in non-centrosymmetric materials, where ion displacement alters the electric dipole moment. Materials like quartz, zinc oxide, and polyvinylidene fluoride (PVDF) have demonstrated high potential for energy harvesting and sensing.
Advances in crystal structures and composite designs have further enhanced their efficiency, though challenges persist. For instance, piezoceramics are brittle, while piezopolymers, though flexible, offer lower energy conversion efficiency.
One of the key benefits of piezoelectric sensors is their ability to function without external power sources, making them ideal for implantable medical devices and wearable technologies.
These sensors can detect minute dynamic changes in pressure, providing real-time data for health monitoring systems. Enhanced flexibility and sensitivity are critical for their integration into applications such as soft robotics and human-machine interfaces.
Triboelectric effects, on the other hand, rely on contact and separation between materials with different electronegativities, generating voltage through charge transfer. Materials like polytetrafluoroethylene (PTFE) and polydimethylsiloxane (PDMS) are frequently used due to their high charge transfer efficiency.
These sensors deliver robust performance, even at low frequencies, and are easily integrated into flexible designs. However, their sensitivity to environmental conditions, such as humidity, poses significant challenges.
Triboelectric sensors are particularly valuable in low-power applications where environmental energy harvesting, such as vibration or motion, can sustain their operation.
These sensors’ ability to integrate with environmentally friendly materials further positions them as key components in sustainable technology development. By combining these principles, researchers are unlocking novel possibilities for self-powered devices across various industries.
Improving piezoelectric and triboelectric sensor performance hinges on innovative manufacturing strategies. For piezoelectric materials, enhancing the piezoelectric constant is key. This parameter, which measures electrical charge generation per unit of mechanical stress, can be optimized through doping, crystallinity control, and the integration of composite structures. Researchers are also exploring lead-free ceramics and polymer blends to create eco-friendly and flexible sensors.
Related Stories
Innovative techniques like the poling process play a critical role in aligning the dipoles within piezoelectric materials. This alignment is achieved by applying a strong DC electric field slightly below the material’s Curie temperature, enhancing the material’s overall polarization.
Advances in material engineering have enabled the development of hybrid structures, which combine the mechanical strength of ceramics with the flexibility of polymers, offering a balance of performance and adaptability.
Triboelectric sensors benefit from surface modification techniques like plasma treatments and microstructuring. These methods increase charge transfer efficiency, resulting in durable sensors with high output voltage. Additionally, hybrid materials and nanostructures have shown promise in enhancing performance while maintaining flexibility and resilience to environmental factors.
Recent advancements in 3D printing and solvent-based crystallization techniques have revolutionized sensor design. These methods enable precise control over material properties, enhancing sensitivity and adaptability.
For example, 3D-printed piezoelectric sensors can achieve tailored mechanical dimensions, optimizing performance for specific applications. Similarly, surface treatments in triboelectric sensors improve their ability to operate under varied environmental conditions, broadening their application scope.
The integration of tactile sensors into everyday technology is transforming industries. In healthcare, wearable sensors monitor vital signs with remarkable accuracy. These devices are being developed to detect subtle physiological changes, such as variations in blood pressure or glucose levels, providing a lifeline for patients managing chronic illnesses. Their application extends to prosthetics, where they enable the seamless control of robotic limbs, mimicking natural movement and tactile feedback.
Robotic systems equipped with these sensors achieve fine motor control, enabling tasks that require precision, such as surgical procedures. These systems are instrumental in advancing minimally invasive surgery, where real-time tactile feedback ensures patient safety. Furthermore, their role in assistive technologies, such as robotic exoskeletons, enhances mobility for individuals with physical disabilities, bridging the gap between humans and machines.
Touchscreens and human-machine interfaces benefit from the high sensitivity of piezoelectric and triboelectric sensors, ensuring seamless interaction. In consumer electronics, these sensors enhance user experience by enabling pressure-sensitive touch functionality. Gaming and virtual reality applications stand to gain from these advancements, providing immersive environments where tactile feedback enhances realism.
Artificial intelligence (AI) further amplifies the potential of these technologies. By analyzing tactile inputs like texture and pressure, AI-driven systems can enhance sensor accuracy and functionality. For instance, AI-integrated sensors can distinguish between subtle changes in surface texture, a critical capability for advanced robotic systems. AI-based algorithms also play a pivotal role in processing data from multiple sensors, enabling multi-modal sensing capabilities.
Environmental monitoring is another area where these sensors shine. By detecting vibrations, temperature changes, or pressure variations, piezoelectric and triboelectric sensors contribute to predictive maintenance in industrial settings. Their integration into smart city infrastructure supports real-time monitoring of critical systems, such as bridges and pipelines, ensuring safety and sustainability.
Despite significant progress, several hurdles remain. Piezoelectric materials must overcome brittleness and limited energy conversion efficiency, while triboelectric sensors require solutions to environmental sensitivity. Researchers are addressing these challenges through interdisciplinary approaches, combining material science, engineering, and AI.
The potential for multimodal sensing—where sensors simultaneously detect various stimuli—is a promising avenue. By decoupling responses from multiple stimuli, such as pressure and temperature, sensors can achieve greater accuracy and reliability. Moreover, AI-based systems enable real-time processing of complex tactile inputs, paving the way for intelligent devices that mimic human sensory capabilities.
Professor Hanjun Ryu of Chung-Ang University, South Korea, has been at the forefront of this research. His team’s work, published in the International Journal of Extreme Manufacturing, provides a comprehensive overview of material and device fabrication strategies. “Our study explains the materials and device fabrication strategies for tactile sensors using piezoelectric and triboelectric effects, as well as the types of sensory recognition,” says Prof. Ryu.
Their findings highlight the importance of combining innovative material engineering with advanced manufacturing techniques. By leveraging these strategies, researchers can develop high-performance sensors capable of real-time interaction and multi-modal sensing. The potential for creating flexible, stretchable, and biocompatible sensors opens new possibilities for in-vivo applications and wearable technologies, enhancing human-machine integration.
The integration of tactile sensors into intelligent systems marks a significant leap forward in technology. From healthcare to robotics, these sensors are transforming how machines interact with their environment. By addressing current limitations and exploring new opportunities, researchers are paving the way for a future where technology seamlessly integrates with human needs.
The synergy between AI and sensor technology is driving the development of next-generation tactile systems. AI-based multi-sensory analysis enables precise texture and pressure recognition, facilitating advancements in robotics, prosthetics, and consumer electronics. These innovations promise to redefine industries, creating devices that emulate human touch with unprecedented accuracy.
As Prof. Ryu concludes, “It is anticipated that AI-based multi-sensory sensors will make innovative contributions to such advancements in various fields.” This vision underscores the transformative potential of piezoelectric and triboelectric technologies, promising a new era of intelligent, human-centric devices.
With continued research and development, these sensors are poised to become indispensable in addressing the challenges of tomorrow.
Note: Materials provided above by The Brighter Side of News. Content may be edited for style and length.
Like these kind of feel good stories? Get The Brighter Side of News' newsletter.
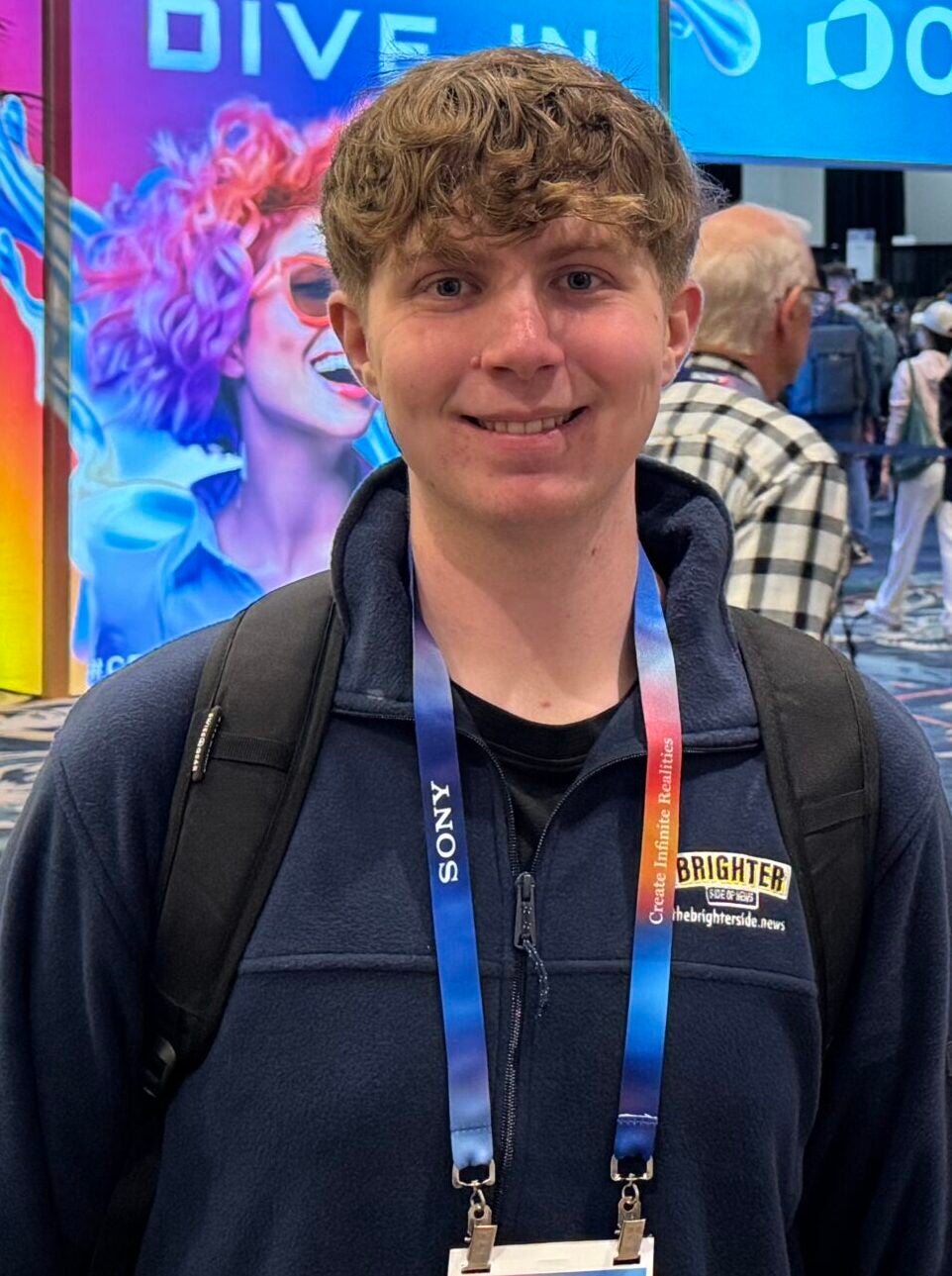
Joshua Shavit
Science & Technology Writer | AI and Robotics Reporter
Joshua Shavit is a Los Angeles-based science and technology writer with a passion for exploring the breakthroughs shaping the future. As a contributor to The Brighter Side of News, he focuses on positive and transformative advancements in AI, technology, physics, engineering, robotics and space science. Joshua is currently working towards a Bachelor of Science in Business Administration at the University of California, Berkeley. He combines his academic background with a talent for storytelling, making complex scientific discoveries engaging and accessible. His work highlights the innovators behind the ideas, bringing readers closer to the people driving progress.