Scientists turn low-value plastic waste into high-grade, valuable products
Millions of Americans dutifully separate their recyclable, plastic waste into the designated bins with hopes of a sustainable future.
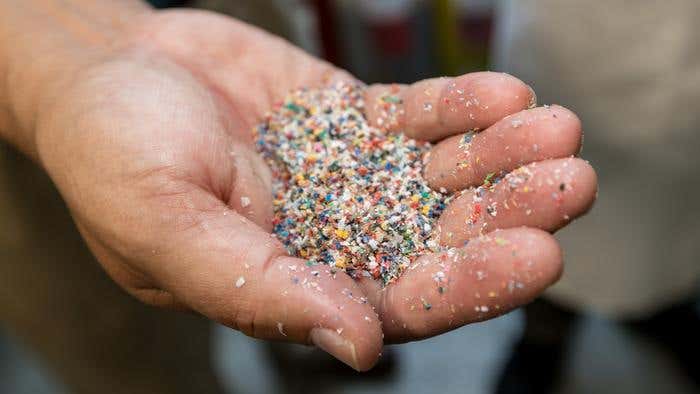
[Aug. 11, 2023: Staff Writer, The Brighter Side of News]
Low-value waste plastic can be converted into high-value chemicals in a new process developed by UW–Madison researchers. (CREDIT: Joel Hallberg)
Every week, millions of Americans dutifully separate their recyclables, placing their plastic waste into the designated bins with hopes of a sustainable future. Yet, the bitter truth is that conventional mechanical recycling methods fall short when it comes to materials like flexible films, multilayer substances, and many colored plastics. The staggering fact? A mere 9% of U.S plastic is ever recycled, and even then, often into low-grade products.
But all that might be about to change. Chemical engineers from the University of Wisconsin–Madison have unveiled a revolutionary technique that has the potential to turn low-value plastic waste into high-grade, valuable products.
The Science Behind the Revolution:
Detailed in Science, this innovative method could drastically revamp the current economic landscape for plastic recycling and herald a new era where previously non-recyclable plastics can be put to good use. Moreover, the approach may slash greenhouse gas emissions from conventional production of certain industrial chemicals by a remarkable 60%.
The magic begins with pyrolysis – a method where plastics are subjected to intense heat in the absence of oxygen. This produces pyrolysis oil, a rich concoction of various compounds. Among them are olefins, simple hydrocarbons that serve as foundational blocks in the creation of a myriad of chemicals and polymers. These include polyesters, surfactants, alcohols, and carboxylic acids, to name a few.
Related Stories
Present-day manufacturing, using processes like steam cracking, requires massive energy inputs to produce olefins from petroleum. The team from UW–Madison offers an alternative. They recover olefins from pyrolysis oil, subjecting them to a less energy-demanding chemical operation known as homogenous hydroformylation catalysis. This conversion results in the production of aldehydes, which can be further refined into valuable industrial alcohols.
“These products aren't just ordinary; they are higher-value materials used in everyday items like soaps, cleaners, and even more advanced polymers,” explained George Huber, a chemical and biological engineering professor who spearheaded the research. Huber was ably assisted in this venture by postdoctoral researcher Houqian Li and PhD student Jiayang Wu.
The Implications and Market Potential:
Huber, also at the helm of the Department of Energy-funded Center for the Chemical Upcycling of Waste Plastics, expressed his enthusiasm, “It’s a groundbreaking technology to elevate plastic waste using hydroformylation chemistry.”
Using a process called hydroformylation, Professor George Huber (left) and postdoctoral researcher Houqian Li are able to recover the olefins in an oil made from waste plastic and transform them into high-value chemicals. (CREDIT: Joel Hallberg)
The ripple effects in the recycling industry could be felt soon. A handful of major chemical corporations in recent times have either constructed or announced the development of facilities dedicated to extracting pyrolysis oils from discarded plastics. Yet, many of these companies have resorted to using the traditional steam crackers, resulting in lower-value compounds. This novel chemical recycling approach could offer a more sustainable and profitable avenue for these oils.
Li emphasized the economic upside, stating, “Current industry practices don't fully exploit the potential of pyrolysis oil. With our method, we can derive high-value alcohols priced between $1,200 to $6,000 per ton from waste plastics that typically hold a meager value of approximately $100 per ton. Moreover, our process isn't reinventing the wheel. It seamlessly integrates with existing technology, facilitating scalability.”
George Huber is a professor of chemical and biological engineering at the University of Wisconsin–Madison. (CREDIT: University of Wisconsin–Madison)
This study stands as a testament to the collaborative spirit of the UW–Madison community. Clark Landis, chair of the Department of Chemistry and a leading authority on hydroformylation, proposed applying the method to pyrolysis oils. Chemical and biological engineering professor Manos Mavarikakis offered crucial molecular-level insights, while another professor from the same department, Victor Zavala, played an instrumental role in evaluating the economic aspects and lifecycle of plastic waste.
The journey isn’t over for Huber and his team. They are now immersed in refining the process, delving deeper into understanding how various recycled plastics and catalysts culminate in specific chemical products. Huber concludes with a note of optimism, “The potential avenues we can explore with this platform are vast. We’re looking at a vast market for our products. This could truly revolutionize the plastic recycling domain.”
For more environmental news stories check out our Green Impact section at The Brighter Side of News.
Note: Materials provided above by The Brighter Side of News. Content may be edited for style and length.
Like these kind of feel good stories? Get the Brighter Side of News' newsletter.
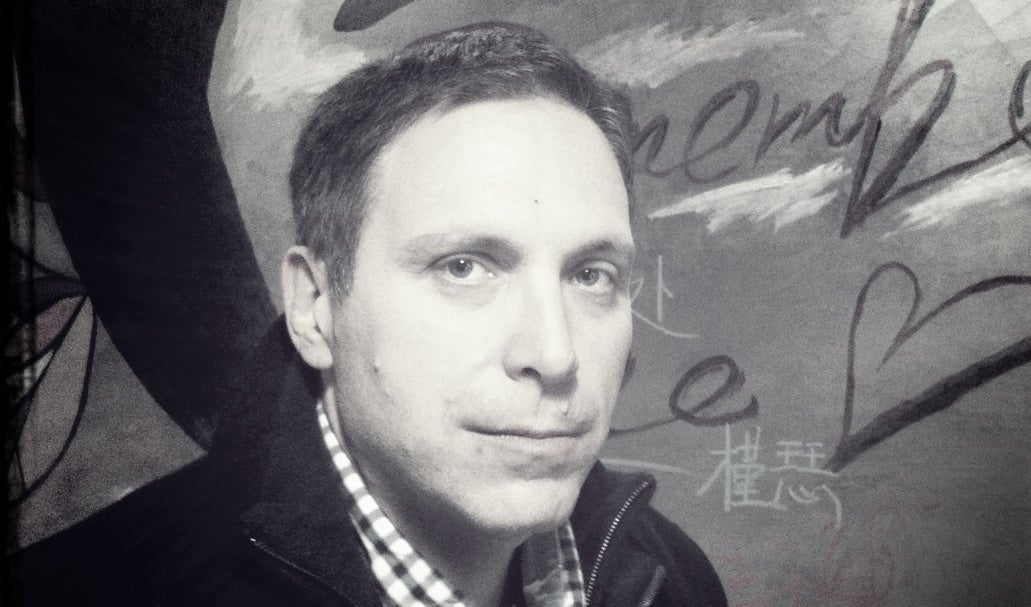
Joseph Shavit
Head Science News Writer | Communicating Innovation & Discovery
Based in Los Angeles, Joseph Shavit is an accomplished science journalist, head science news writer and co-founder at The Brighter Side of News, where he translates cutting-edge discoveries into compelling stories for a broad audience. With a strong background spanning science, business, product management, media leadership, and entrepreneurship, Joseph brings a unique perspective to science communication. His expertise allows him to uncover the intersection of technological advancements and market potential, shedding light on how groundbreaking research evolves into transformative products and industries.