Scientists developed smart robotic materials that can reshape themselves like living tissues
Scientists have created robotic materials that mimic living cells, allowing them to reshape and adapt like biological tissues.
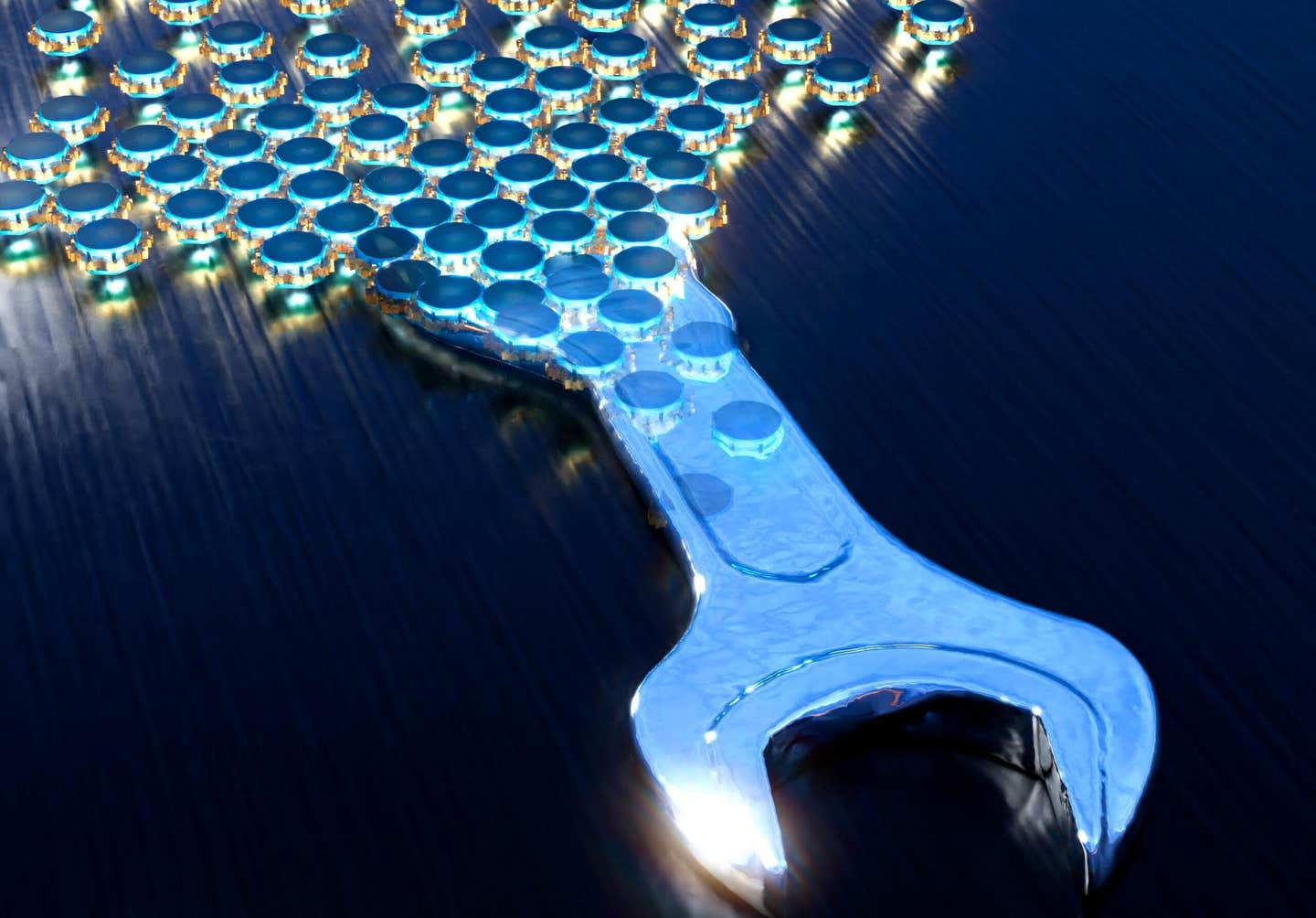
Disk-shaped robots can act collectively to accomplish tasks such as lifting and manipulating objects, or supporting weight. (CREDIT: Brian Long / UCSB)
Scientists are working on a groundbreaking concept—robotic materials that can reshape themselves and change their properties, much like living tissues.
Unlike traditional materials that remain fixed once formed, these robotic materials have the ability to become rigid or fluid-like on demand. This innovation could lead to structures that transform their shape and function without external force, revolutionizing manufacturing, construction, and even medicine.
Researchers at the University of California, Santa Barbara, and TU Dresden have developed a proof-of-concept robotic system inspired by biological processes. Their findings were published in the journal Science.
"We've figured out a way for robots to behave more like a material," said Matthew Devlin, a former doctoral researcher at UCSB. His team has created a collective of small, disk-shaped robots that can assemble into different formations and change their mechanical properties, much like living cells do during development.
One of the biggest challenges in designing such a system is making the material both strong and adaptable. Conventional industrial processes like molding and forging use external heat and pressure to reshape materials.
In contrast, robotic materials must be internally powered and actively controlled to switch between rigid and flowing states at will. "They need to hold a shape but also selectively flow into new forms," explained Elliot Hawkes, a professor of mechanical engineering at UCSB.
Biology as a Blueprint for Robotics
The inspiration for this innovation comes from embryonic development. Living tissues have an extraordinary ability to self-organize, self-heal, and control their mechanical strength in space and time.
Otger Campàs, a physicist formerly at UCSB and now director at TU Dresden, has studied how embryos shape themselves. "Living embryonic tissues are the ultimate smart materials," he said. His research revealed that developing cells can transition between solid and fluid-like states, allowing an embryo to take shape.
Cells achieve these transformations through three key mechanisms: active forces that move cells around, biochemical signaling that coordinates movements, and cell adhesion that gives the tissue its final form. The research team applied these principles to their robotic system.
Related Stories
Each robot has eight motorized gears along its edge that enable movement in tightly packed spaces, mimicking cellular motion. Instead of biochemical signals, the robots use light sensors with polarized filters to determine movement direction. When exposed to a light field, the polarization tells them which way to turn their gears, allowing the entire system to change shape collectively.
To replicate cell adhesion, the robots use controllable magnets that enable them to stick together or separate as needed. This adhesion allows the robotic material to be strong when necessary but also capable of fluid-like rearrangement.
Engineering Adaptive Robotic Materials
One of the most significant discoveries was the role of signal fluctuations in shaping the robotic material. In biological tissues, fluctuating forces help cells switch between solid and fluid states.
The researchers encoded similar fluctuations into their robots, allowing them to dynamically transition between rigid and flowing behaviors. "We had previously shown that in living embryos, force fluctuations are key to turning a solid-like tissue into a fluid one," Campàs said.
This principle proved crucial. When both the inter-unit forces and the fluctuations increased, the robots behaved more like a flowing material. Once they reached the desired shape, turning off the fluctuations made the system rigid again. "This allows the collective to change shape efficiently," Devlin explained.
An unexpected advantage of this method was energy efficiency. Rather than constantly applying force, the robots used fluctuations to achieve movement with lower power consumption. "It’s an interesting result that we didn’t anticipate but discovered when we analyzed the robot behaviors," Hawkes said. This finding could be essential for developing robots that need to operate on limited energy sources.
By controlling which sections of the robotic material activate their dynamic forces, researchers could fine-tune the system’s properties. Some areas remained stiff while others became fluid, enabling the material to support heavy loads, reshape itself, manipulate objects, and even self-heal.
This ability to modulate material states in real time could lead to innovations in areas such as robotic surgery, reconfigurable architecture, and adaptable prosthetics.
Scaling Up and Future Possibilities
The current prototype consists of 20 relatively large robotic units, but simulations suggest that the system could be scaled to thousands of miniaturized units. Former postdoctoral fellow Sangwoo Kim, now a professor at EPFL, has modeled how smaller units could create even more seamless material-like behavior.
Beyond robotics, the study of these systems could provide new insights into physics, particularly in areas like phase transitions and active matter mechanics. The ability to engineer programmable materials may also refine hypotheses in biological research. By combining these systems with machine learning, researchers hope to unlock new emergent behaviors in robotic materials that have yet to be explored.
With continued advancements, robotic materials could redefine what’s possible in technology. A future where objects adapt dynamically to their environment—where bridges can repair themselves, clothing adjusts its fit in real time, or medical implants reconfigure inside the body—may not be far off.
Note: Materials provided above by The Brighter Side of News. Content may be edited for style and length.
Like these kind of feel good stories? Get The Brighter Side of News' newsletter.
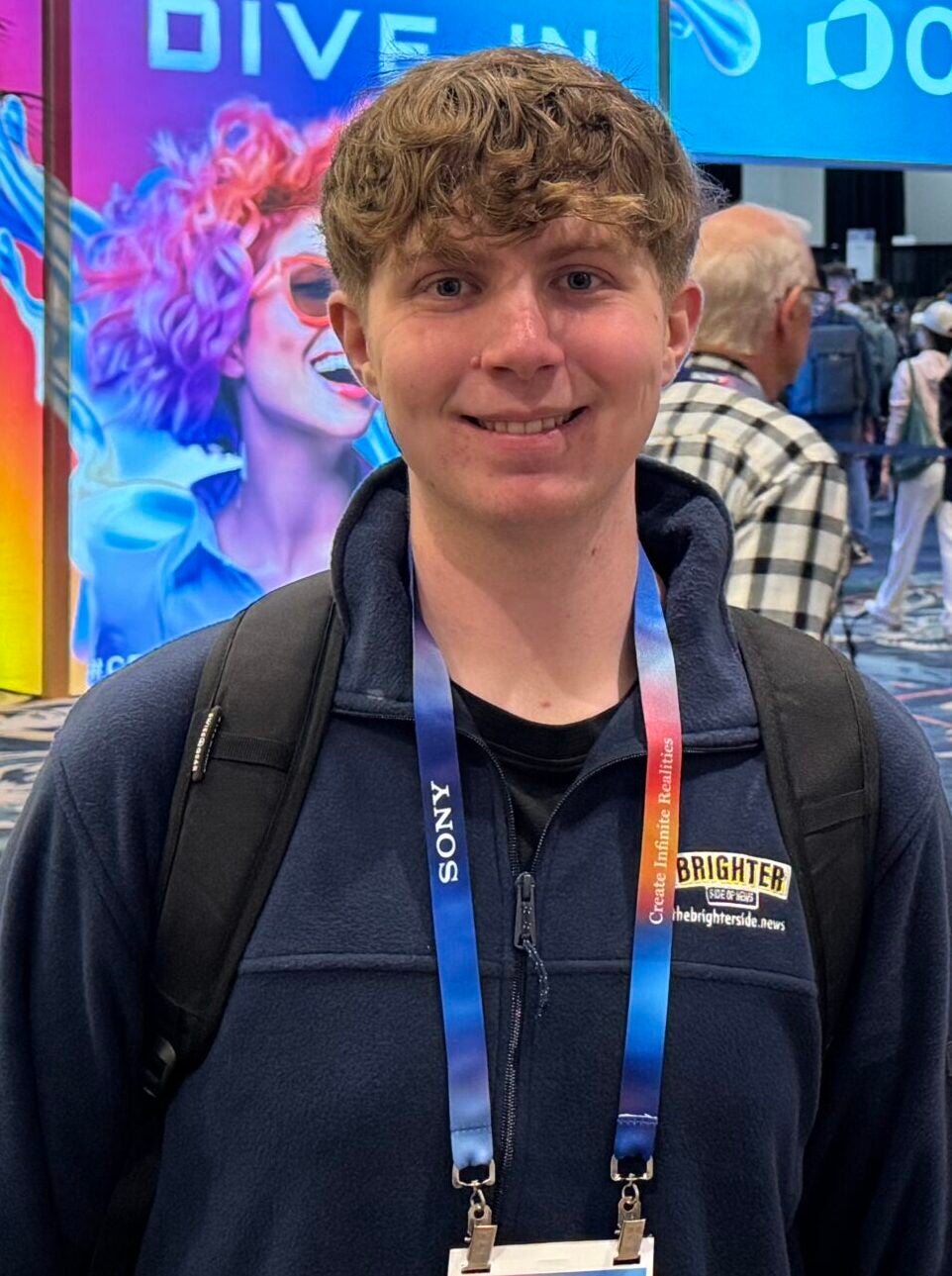
Joshua Shavit
Science & Technology Writer | AI and Robotics Reporter
Joshua Shavit is a Los Angeles-based science and technology writer with a passion for exploring the breakthroughs shaping the future. As a contributor to The Brighter Side of News, he focuses on positive and transformative advancements in AI, technology, physics, engineering, robotics and space science. Joshua is currently working towards a Bachelor of Science in Business Administration at the University of California, Berkeley. He combines his academic background with a talent for storytelling, making complex scientific discoveries engaging and accessible. His work highlights the innovators behind the ideas, bringing readers closer to the people driving progress.