Scientists develop cheap and effective way to trap carbon in common rocks
Scientists have found a scalable way to capture CO₂ using minerals, offering a low-cost, high-impact solution to climate change.
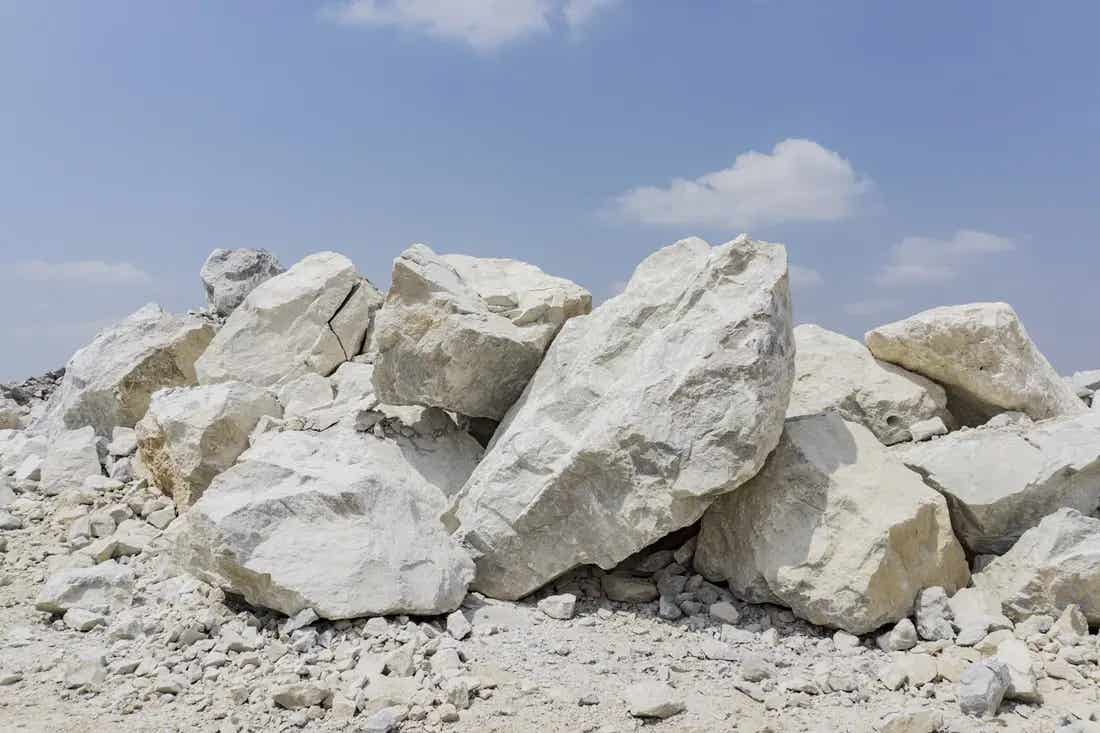
Researchers have developed a way to rapidly capture CO₂ using heated minerals. (CREDIT: CC BY-SA 4.0)
Reducing carbon dioxide (CO₂) in the atmosphere is critical to slowing global warming. While direct air capture (DAC) technology has gained attention, it remains expensive and energy-intensive, requiring up to 2.7 megawatt-hours per ton of CO₂ captured.
An alternative method, called enhanced weathering, could offer a more scalable and affordable solution by using Earth’s natural minerals.
At Stanford University, chemists have developed a method to speed up the natural reaction of silicate minerals with CO₂. By heating minerals in kilns, they create highly reactive materials that rapidly absorb CO₂ from the air and permanently store it. This process, which mimics a technique used in cement production, could make large-scale carbon removal practical. The team's research findings were published in the journal Nature.
“The Earth has an inexhaustible supply of minerals that are capable of removing CO₂ from the atmosphere, but they just don’t react fast enough on their own to counteract human greenhouse gas emissions,” said Matthew Kanan, a Stanford chemistry professor. “Our work solves this problem in a way that we think is uniquely scalable.”
The Science Behind Enhanced Weathering
In nature, minerals such as olivine, serpentine, and pyroxenes slowly react with CO₂ and water to form stable bicarbonate and carbonate minerals. This process, known as weathering, removes about 0.5 gigatons of CO₂ annually. However, the reaction occurs over thousands of years, making it too slow to offset human emissions.
The Stanford researchers developed a way to speed up this reaction. They heated calcium oxide (a common material in cement production) with magnesium silicates in a furnace. This caused the minerals to swap ions and form magnesium oxide and calcium silicate—two highly reactive materials that absorb CO₂ much faster.
“The process acts as a multiplier,” Kanan explained. “You take one reactive mineral, calcium oxide, and a magnesium silicate that is more or less inert, and you generate two reactive minerals.”
Related Stories
In laboratory tests, these minerals removed CO₂ at astonishing speeds. When exposed to pure CO₂ and water, they fully transformed into carbonates within two hours. In conditions mimicking real-world air exposure, the process took weeks to months—still thousands of times faster than natural weathering.
Scaling Up for Global Impact
For this method to significantly impact climate change, it must be deployed on a massive scale. Current cement kilns can be adapted to produce these reactive minerals, and the raw materials needed are abundant. More than 400 million tons of silicate-rich mine tailings are generated worldwide each year, offering a vast supply for processing.
Jonathan Fan, a Stanford electrical engineering professor, is working with Kanan’s team to develop electric-powered kilns. This would eliminate emissions from fossil fuels currently used to heat conventional kilns.
Each ton of processed mineral is expected to remove one ton of CO₂ from the air, even after accounting for emissions from energy use. Considering that fossil fuel emissions surpassed 37 billion tons in 2024, large-scale adoption could play a significant role in reducing atmospheric carbon levels.
“You can imagine spreading magnesium oxide and calcium silicate over large land areas to remove CO₂ from ambient air,” Kanan said. “One exciting application that we’re testing now is adding them to agricultural soil.”
Potential Agricultural Benefits
Beyond carbon removal, this process could also improve soil health. Farmers frequently add calcium carbonate to fields to regulate pH levels, a process known as liming. The minerals developed at Stanford could serve the same purpose while also capturing CO₂.
“Adding our product would eliminate the need for liming since both mineral components are alkaline,” Kanan explained. “In addition, as calcium silicate weathers, it releases silicon to the soil in a form that the plants can take up, which can improve crop yields and resilience.”
If these benefits prove effective, farmers might pay for these minerals as a soil treatment, helping offset the costs of large-scale carbon removal. This economic incentive could accelerate adoption and drive meaningful reductions in atmospheric CO₂.
A Future Built on Carbon Capture
The new mineral-processing method developed at Stanford could revolutionize carbon removal. Unlike DAC, which requires costly infrastructure and high energy input, this approach builds on well-established industrial processes. By using existing kiln designs, the transition from laboratory success to real-world implementation appears feasible.
“Society has already figured out how to produce billions of tons of cement per year, and cement kilns run for decades,” Kanan said. “If we use those learnings and designs, there is a clear path for how to go from lab discovery to carbon removal on a meaningful scale.”
With an estimated 100,000 gigatons of olivine and serpentine reserves available, this technique could remove far more CO₂ than humans have ever emitted. If successfully deployed, it could become a cornerstone of global efforts to fight climate change.
Note: Materials provided above by The Brighter Side of News. Content may be edited for style and length.
Like these kind of feel good stories? Get The Brighter Side of News' newsletter.
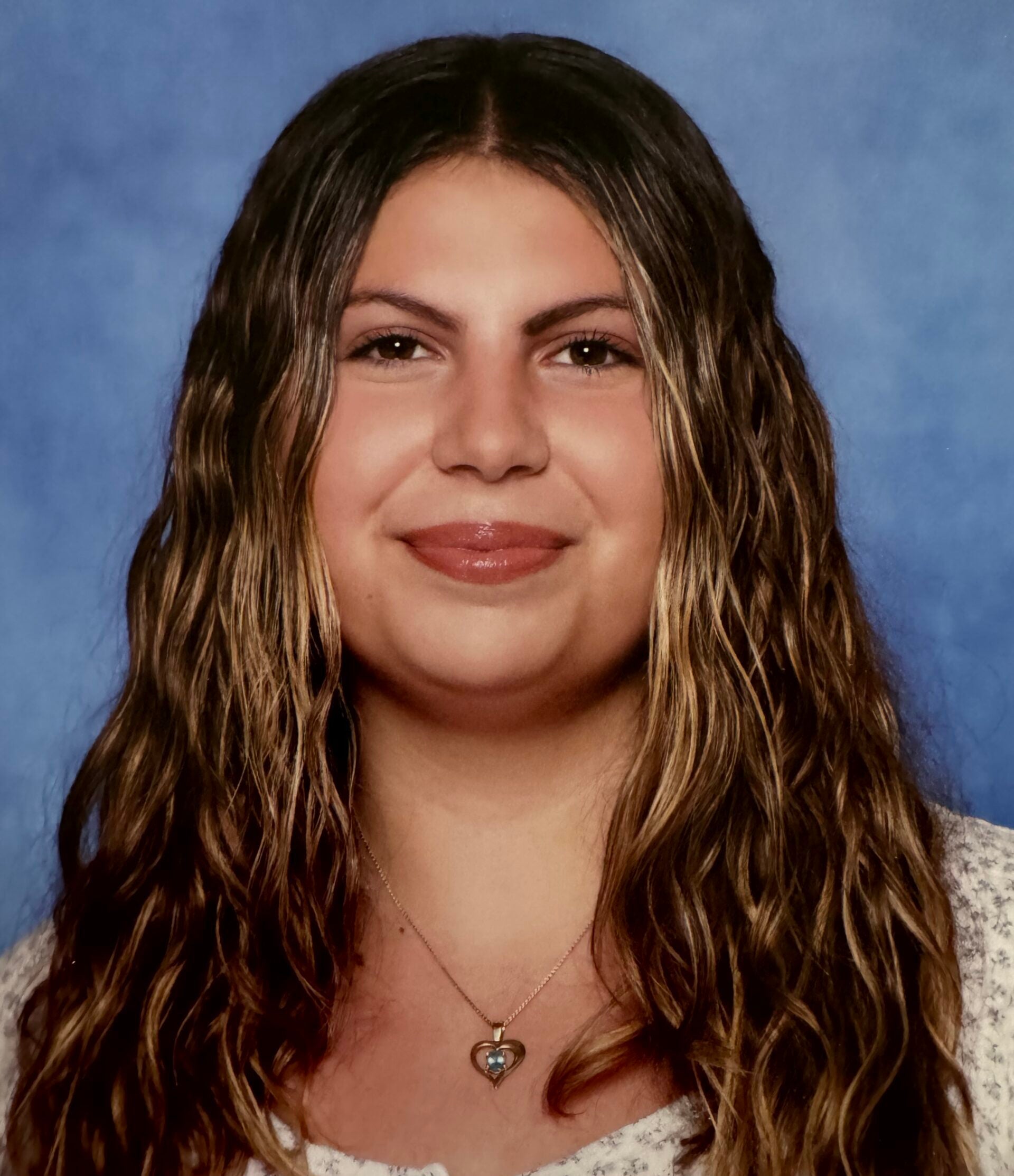
Rebecca Shavit
Science & Technology Journalist | Innovation Storyteller
Based in Los Angeles, Rebecca Shavit is a dedicated science and technology journalist who writes for The Brighter Side of News, an online publication committed to highlighting positive and transformative stories from around the world. With a passion for uncovering groundbreaking discoveries and innovations, she brings to light the scientific advancements shaping a better future. Her reporting spans a wide range of topics, from cutting-edge medical breakthroughs and artificial intelligence to green technology and space exploration. With a keen ability to translate complex concepts into engaging and accessible stories, she makes science and innovation relatable to a broad audience.