Scientists create low-cost green carbon fiber using microwave energy
A new microwave-based process reduces carbon fiber production costs by 70%, making the material more sustainable and widely accessible.
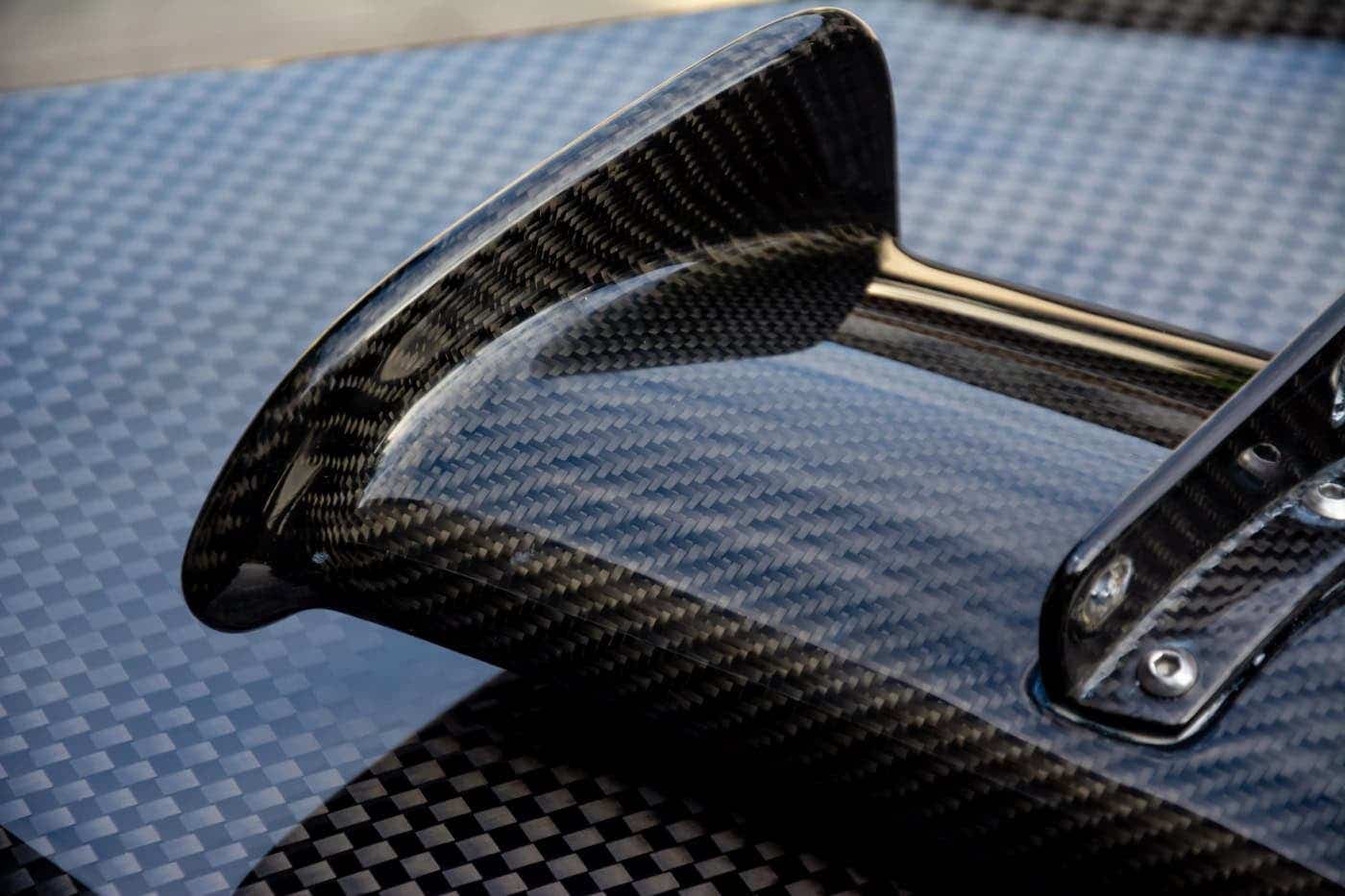
Carbon fiber-reinforced polymers (CFRPs) are essential in industries like automotive. (CREDIT: CC BY-SA 4.0)
Carbon fiber-reinforced polymers (CFRPs) are essential in industries like aerospace, automotive, and renewable energy due to their strength, lightweight nature, and chemical resistance. However, their production is costly and highly energy-intensive—up to 14 times more energy-demanding than steel. The high cost limits carbon fiber use to high-end applications, but a revolutionary new method could change that.
A research team at the University of Limerick (UL) has introduced a breakthrough approach to manufacturing carbon fiber.
Their project, CARBOWAVE, uses plasma and microwave heating instead of conventional thermal processing. This new technique reduces energy consumption by 70% while maintaining the material’s strength. The potential impact extends across industries, making carbon fiber more accessible and sustainable.
The Challenge of Traditional Carbon Fiber Production
The high cost of carbon fiber primarily stems from its production process. It starts with polyacrylonitrile (PAN), a synthetic polymer, which undergoes a series of transformations to become carbon fiber. This includes stabilization and carbonization stages, requiring temperatures above 1,000°C. Traditional heating methods demand enormous amounts of electricity and natural gas, contributing to high costs and carbon emissions.
For decades, researchers have sought alternatives to PAN, experimenting with biobased polymers like lignin. However, these substitutes fail to match the mechanical performance of PAN-based carbon fibers.
The need for a more efficient manufacturing process has driven scientists toward alternative heating methods, culminating in the CARBOWAVE project’s innovative approach.
Related Stories
Harnessing Microwave Technology for Sustainability
The key to this new process is microwave-assisted heating. While microwaves have been used to synthesize nanoparticles and graphene, applying them to carbon fiber production is groundbreaking. However, PAN and lignin do not naturally absorb microwave energy, presenting a challenge.
To solve this, the UL research team developed a method using carbon-based nanomaterials as susceptors—substances that absorb microwaves and convert the energy into heat.
Carbon nanotubes (MWCNTs) were selected due to their high microwave absorption and uniform distribution on fiber surfaces. When exposed to microwave radiation, these nanotubes heat the fibers rapidly and efficiently.
This method eliminates the need for prolonged high-temperature treatments, making the process faster and significantly less energy-intensive. Additionally, microwave heating offers advantages such as selective heating, better energy transfer, and automation potential, further streamlining production.
Professor Maurice Collins, principal investigator on the project, emphasized the significance of this advancement:
“Europe’s reliance on energy-intensive processes has long been a barrier to achieving sustainability. CARBOWAVE addresses this challenge and offers the potential to produce more sustainable and cheaper carbon fiber.”
Industry Implications and Future Potential
Carbon fiber is a strategic material for Europe’s energy future, playing a critical role in wind turbines, lightweight electric vehicles, and hydrogen storage. Reducing its production cost and environmental impact will allow broader applications, from construction and transportation to green energy infrastructure.
Co-principal investigator Dr. Anne Beaucamp McLoughlin highlighted the project's far-reaching implications:
“This project will allow carbon fiber production to be more energy-efficient, faster, and cheaper while significantly reducing its environmental footprint.”
One of the most surprising findings of the research was that carbon fiber could be produced using a standard household microwave while maintaining mechanical properties comparable to those made with traditional methods. This discovery underscores the efficiency of the microwave-based process and its potential scalability.
CARBOWAVE's impact extends beyond energy savings. By reducing carbon emissions and dependence on fossil fuels, it aligns with global efforts to combat climate change. The project also strengthens Europe's position in the advanced materials market, where it currently holds 37% of the global share.
Professor Collins reinforced the project's transformative nature:
“This project promises to unlock the broader industrial use of carbon fiber by drastically reducing its production costs and environmental footprint.”
CARBOWAVE brings together leading research institutions and industry partners across Europe. UL collaborates with the Deutsche Institute für Textil- und Faserforschung in Germany, the University of Valencia in Spain, Fraunhofer IFAM in Germany, and companies such as Microwave Technologies Consulting SAS in France, Muegge GmbH in Germany, Centro Ricerche Fiat in Italy, Juno Composite Ltd in Ireland, and Eirecomposites Ltd.
By integrating plasma and microwave heating technologies, CARBOWAVE is poised to revolutionize carbon fiber production, making the material more sustainable and widely available for future technological advancements.
Note: Materials provided above by The Brighter Side of News. Content may be edited for style and length.
Like these kind of feel good stories? Get The Brighter Side of News' newsletter.
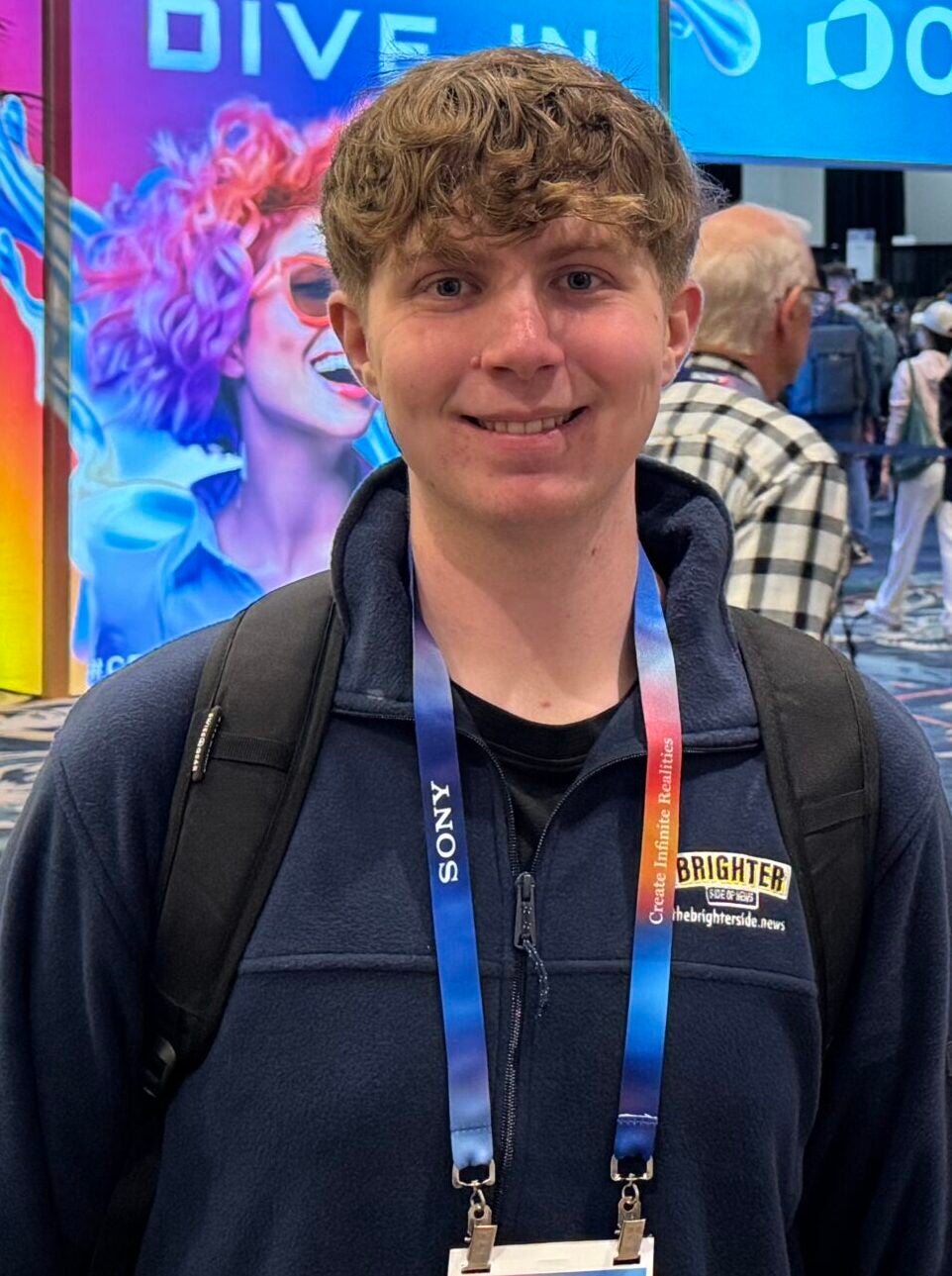
Joshua Shavit
Science & Technology Writer | AI and Robotics Reporter
Joshua Shavit is a Los Angeles-based science and technology writer with a passion for exploring the breakthroughs shaping the future. As a contributor to The Brighter Side of News, he focuses on positive and transformative advancements in AI, technology, physics, engineering, robotics and space science. Joshua is currently working towards a Bachelor of Science in Business Administration at the University of California, Berkeley. He combines his academic background with a talent for storytelling, making complex scientific discoveries engaging and accessible. His work highlights the innovators behind the ideas, bringing readers closer to the people driving progress.