Scientists create lightweight, eco-friendly, building material using molds and fungi
Researchers have devised a groundbreaking method to fabricate building materials using a combination of knitted molds and fungi.
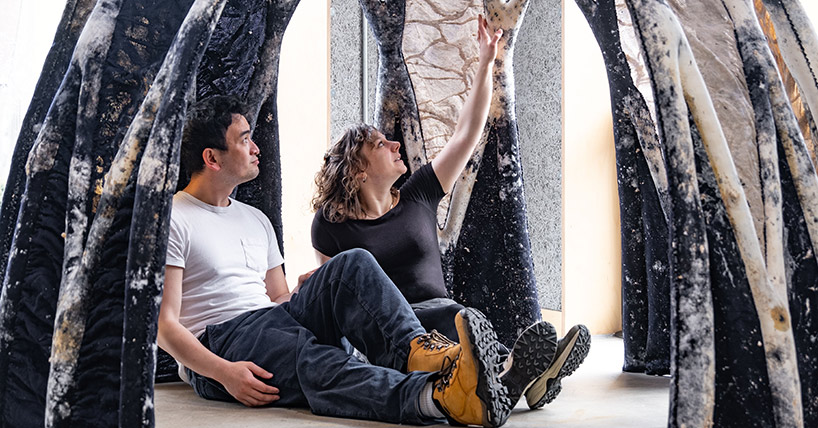
Researchers have devised a groundbreaking method to fabricate building materials using a combination of knitted molds and the root network of fungi. (CREDIT: Hub or Biotechnology in the Built Environment)
Researchers have devised a groundbreaking method to fabricate building materials using a combination of knitted molds and the root network of fungi. This innovative approach, which harnesses the power of mycelium, holds promise for reducing the environmental footprint of construction projects while offering enhanced strength and versatility in material design.
Mycocrete, as it's been coined, marks a significant advancement in the realm of biomaterials. Unlike previous attempts utilizing fungal-based composites, mycocrete surpasses limitations associated with shape and growth constraints, paving the way for a diverse range of applications in lightweight, eco-friendly construction.
Dr. Jane Scott from Newcastle University, the corresponding author of the paper published in Frontiers in Bioengineering and Biotechnology, expressed excitement about the potential of mycocrete. "Our ambition is to transform the look, feel, and wellbeing of architectural spaces using mycelium in combination with biobased materials," she stated.
BioKnit mycelium vault. (CREDIT: Hub or Biotechnology in the Built Environment)
The research, conducted by a multidisciplinary team comprising designers, engineers, and scientists from the Living Textiles Research Group, is part of the Hub for Biotechnology in the Built Environment. Funded by Research England, this collaborative effort between Newcastle and Northumbria Universities aims to revolutionize construction practices.
Mycelium, the root network of fungi, serves as the key ingredient in creating these innovative composites. By mixing mycelium spores with a substrate they can feed on, researchers form a paste-like mixture that is then packed into molds.
Under optimal conditions of darkness, humidity, and warmth, the mycelium proliferates, binding the substrate together. This process yields a durable material, akin to conventional construction materials like foam, timber, and plastic, but with significantly lower environmental impact.
Related Stories
However, conventional rigid molds impose limitations on the size and shape of mycelium-based composites due to the organism's need for oxygen.
Knitted textiles present a solution to this challenge, offering oxygen-permeable molds that can adapt from flexible to stiff as the mycelium grows. Scott highlighted the versatility of knitting technology, emphasizing its ability to create seamless 3D structures with minimal waste.
To optimize the mycocrete production process, the researchers developed a specialized paste containing mycelium, paper powder, fiber clumps, water, glycerin, and xanthan gum. This paste, injected into the knitted formwork using a delivery system, ensured consistent packing while maintaining the material's structural integrity.
BioKnit self-supporting structure exhibited in the OME, Newcastle University (CREDIT: Hub for Biotechnology in the Built Environment)
Samples of mycocrete were subjected to rigorous strength tests, including tension, compression, and flexion, demonstrating superior performance compared to conventional mycelium composites.
The porous nature of the knitted formwork facilitated better oxygen availability, resulting in reduced shrinkage during drying and more predictable manufacturing outcomes.
Specimen failure in bending and tension. Sample types 1 to 4 are shown from left to right. Sample type 3 (mycopaste with no textile formwork) exhibits brittle failure and cracks in both bending and tension; samples with textile formwork are held together by the textile tube. (CREDIT: Hub for Biotechnology in the Built Environment)
In a remarkable feat of engineering, the team constructed a proof-of-concept prototype structure dubbed BioKnit—a complex, freestanding dome devoid of joins, thanks to the flexible knitted form. Scott emphasized the significance of this achievement, heralding it as a pivotal step towards integrating mycelium and textile biohybrids into construction practices.
"While our current study specifies particular materials and methods," Scott noted, "there is extensive potential for adapting this formulation to various applications." She also highlighted the need for advancements in machine technology to facilitate the integration of textiles into the construction sector.
Demolding process and growth of sample type 3 (mycocrete paste without fabric): Growth within plastic mold entirely on surface area (top left); demolded paste sample with low level of mycelium growth (top centre); after second growth stage (top right); samples with aluminum foil supports, top view after second growth stage (bottom left); turned samples (bottom centre); fully grown samples at the beginning of the drying stage (bottom right). Sample size: 260 × 27 × 42 mm. (CREDIT: Hub for Biotechnology in the Built Environment)
The development of mycocrete represents a paradigm shift in sustainable construction materials. By harnessing the regenerative properties of mycelium and leveraging the versatility of knitting technology, researchers have unlocked a new frontier in eco-friendly architecture.
As efforts continue to refine and expand upon this innovative approach, the prospect of building a greener, more sustainable future becomes increasingly tangible.
For more environmental news stories check out our Green Impact section at The Brighter Side of News.
Note: Materials provided above by the The Brighter Side of News. Content may be edited for style and length.
Like these kind of feel good stories? Get the Brighter Side of News' newsletter.
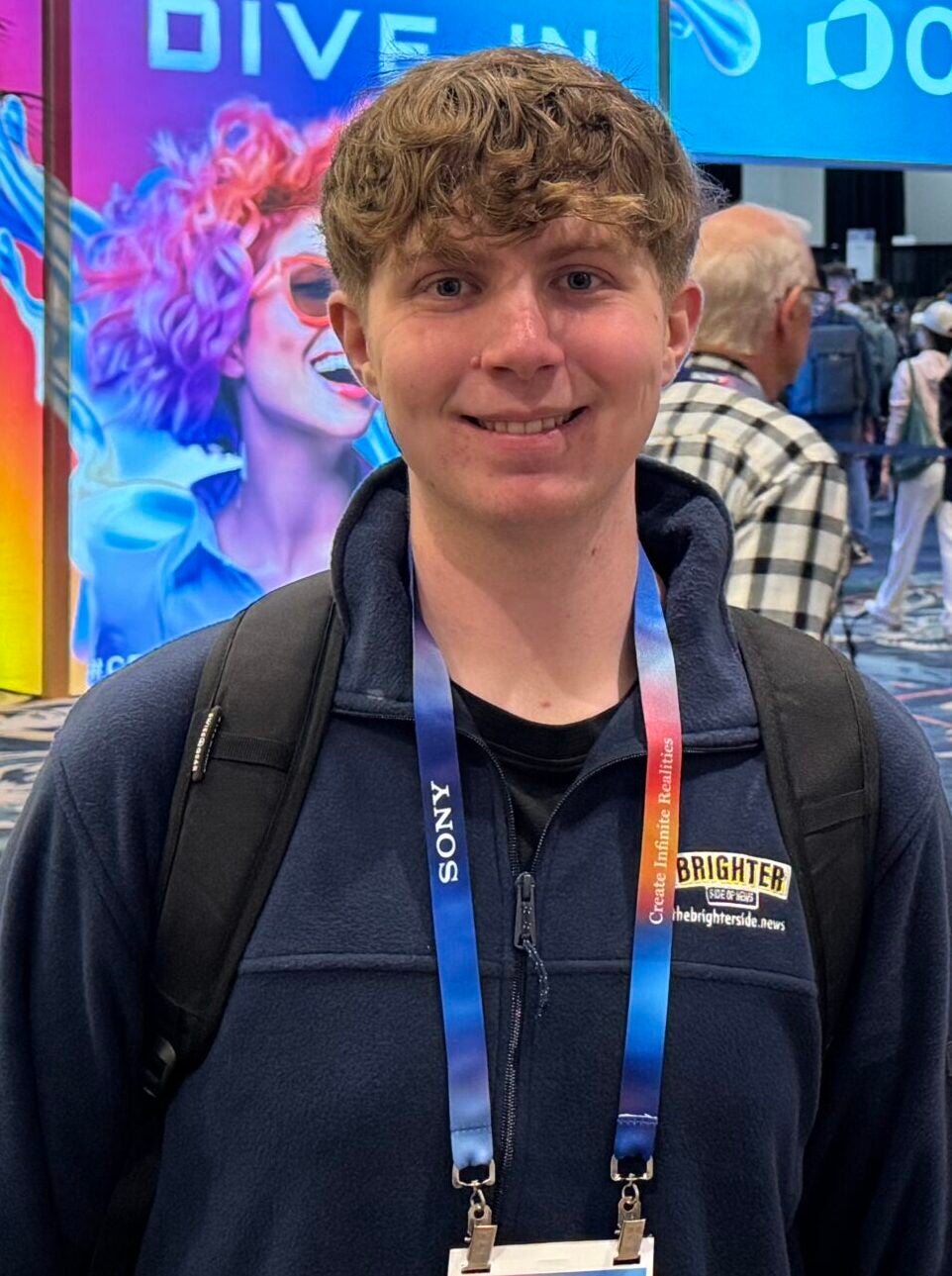
Joshua Shavit
Science & Technology Writer | AI and Robotics Reporter
Joshua Shavit is a Los Angeles-based science and technology writer with a passion for exploring the breakthroughs shaping the future. As a contributor to The Brighter Side of News, he focuses on positive and transformative advancements in AI, technology, physics, engineering, robotics and space science. Joshua is currently working towards a Bachelor of Science in Business Administration at the University of California, Berkeley. He combines his academic background with a talent for storytelling, making complex scientific discoveries engaging and accessible. His work highlights the innovators behind the ideas, bringing readers closer to the people driving progress.