Scientists convert everyday plastics into fully recyclable and potentially biodegradable materials
Instead of drilling for oil and polluting the environment, we’re using stuff that would otherwise be incinerated or left in a landfill.
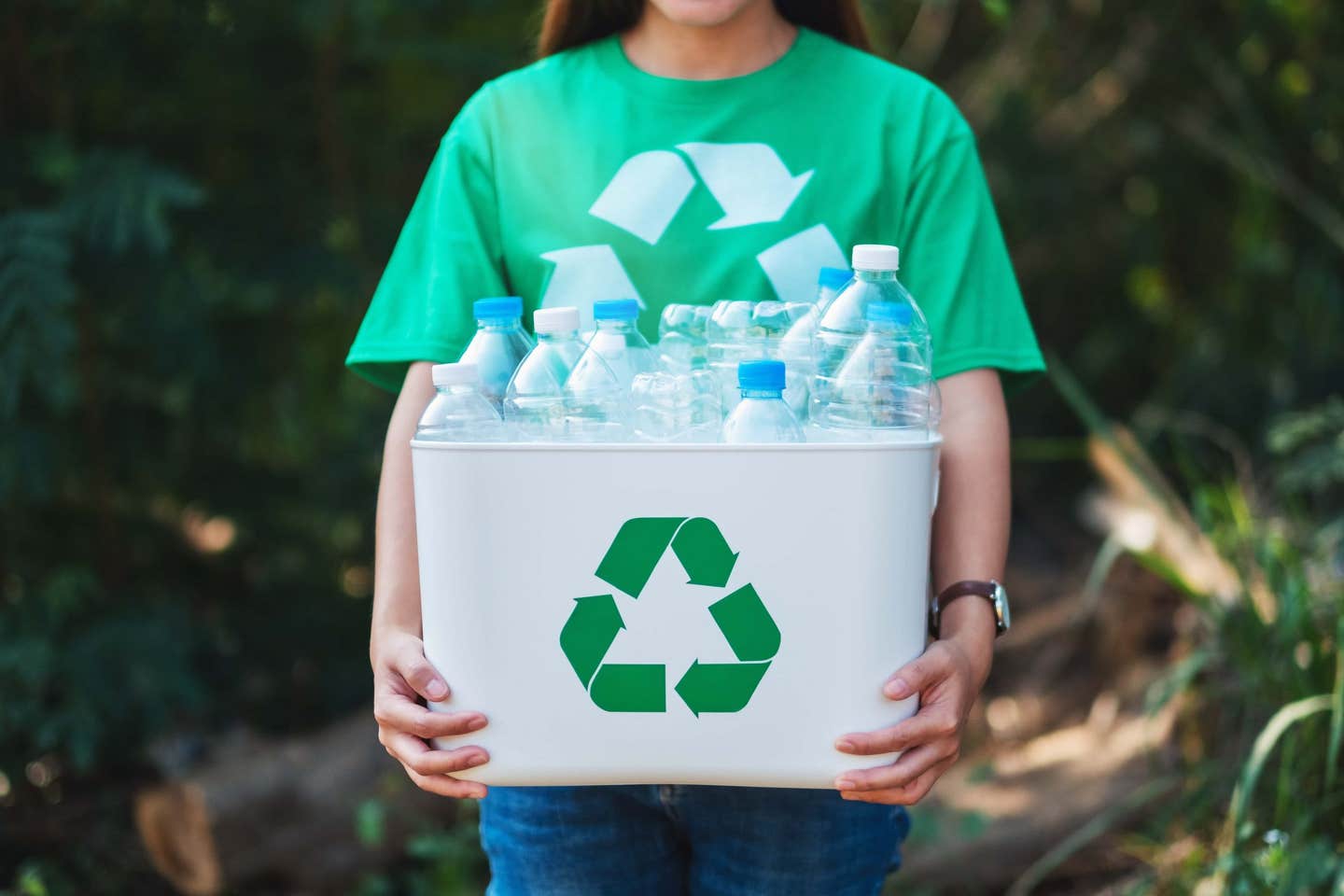
[June 17, 2023: Diana Anderson, DOE/Argonne National Laboratory]
Instead of drilling for oil and polluting the environment, we’re using stuff that would otherwise be incinerated or left in a landfill. (CREDIT: Creative Commons)
Plastics are incredible materials with properties invaluable to the functioning of our modern world. They are strong, flexible, versatile, long-lasting and inexpensive. In particular, high-density polyethylene (HDPE) is ubiquitous in single-use applications such as packaging and containers. You may have seen it labeled with the number two inside the triangular recycling symbol.
But the ways we produce HDPE and our current methods for recycling it pose threats to our own health and that of our planet. Many HDPE products are made from fossil fuels (crude oil, natural gas or coal) and have a massive carbon footprint. And rather than being reused or recycled, most waste HDPE is incinerated, dumped in landfills or left littering the environment. When it is recycled, the quality of the material degrades.
Scientists at the U.S. Department of Energy’s (DOE) Institute for Cooperative Upcycling of Plastics (iCOUP) have developed a new method for recycling HDPE. Using a novel catalytic approach, iCOUP scientists from DOE’s Argonne National Laboratory and Cornell University transformed waste HDPE plastic into a new material that can be recycled repeatedly without loss of quality.
“We are using waste plastic as our source instead of fossil fuels. Instead of drilling for oil and polluting the environment, we’re using stuff that would otherwise be incinerated or left in a landfill.” — Geoffrey Coates, Cornell University
Related Stories
“Plastics are going to be with us forever. They provide functionality that no other material can provide. We need to find ways to reduce the harmful effects of plastic use by improving recyclability,” said Argonne’s Massimiliano Delferro, a scientist on the study.
The team’s new approach converts used HDPE into a fully recyclable and potentially biodegradable material with the same mechanical and thermal properties of the starting single-use plastic. If adopted widely, approaches like this could eventually help to reduce the carbon emission and pollution associated with HDPE.
“We are using waste plastic as our source instead of fossil fuels,” said Cornell’s Geoffrey Coates, a scientist on the study. “Instead of drilling for oil and polluting the environment, we’re using stuff that would otherwise be incinerated or left in a landfill.”
Examples of products made from HDPE. Scientists are converting used products like these into new materials with the same quality and enhanced recyclability. (CREDIT: Shutterstock/JasminkaM)
Like other plastics, HDPE is comprised of long chains of atoms called polymer chains. The team’s new approach uses a series of catalysts — or chemicals that accelerate chemical reactions — to break the HDPE polymer chains into shorter pieces that contain reactive groups of atoms at the ends. Those pieces can then be put back together, or repolymerized, to form new plastic products. The reactive end groups have the added benefit of making the new plastic easier to decompose, both in the lab and potentially in nature.
The Argonne team performed the first round of catalysis on used HDPE products, including water jugs and packaging. The catalysts choose at random which spots to alter in the polymer chains to make them reactive. The longer the scientists leave the HDPE with the catalyst, the more the chains are activated.
Graphical abstract of the chemical recycling route for the conversion of post-consumer high-density polyethylene (HDPE) into telechelic macromonomers suitable for circular reprocessing. (CREDIT: American Chemical Society)
Then, the Cornell team took these activated polymer chains and exposed them to another catalyst. At this stage, the catalyst breaks up the chains and further alters the ends to enable reassembly.
The main challenge was to reproduce the same material properties of HDPE — such as strength and flexibility versus brittleness — in the new material. When the catalysts break up the HDPE, it’s important that there remain enough long polymer chains to bind to each other like threads, making the material more resilient to stress.
When the Cornell team originally repolymerized the catalyzed material, it was much more brittle than the starting HDPE. They then fine-tuned the catalysts to break up the polymer chains in a way that provides a controlled amount of branching when the material is repolymerized. This branching allows chains to form off of the end groups, thereby increasing the average length of the chains in the resulting material. This approach resulted in a material with the same properties as the starting HDPE and greater recyclability.
Proposed chemical recycling of post-consumer HDPE. (CREDIT: American Chemical Society)
Future work will focus on assessing the biodegradability of the new material and reducing the amount of valuable metal used for the catalyst to reduce the overall recycling cost. The team also hopes to apply their strategy to other common plastics.
A paper on the results was published in the Journal of the American Chemical Society.
In addition to Coates and Delferro, authors include Alejandra Arroyave from Argonne and Shilin Cui, Andrew Kocen, Anne LaPointe and Jaqueline Lopez from Cornell University.
This work was supported as part of iCOUP, an Energy Frontier Research Center funded by the DOE Office of Science, Basic Energy Sciences at Argonne and Ames Laboratory.
For more green news stories check out our Green Impact section at The Brighter Side of News.
Note: Materials provided above by DOE/Argonne National Laboratory. Content may be edited for style and length.
Like these kind of feel good stories? Get the Brighter Side of News' newsletter.
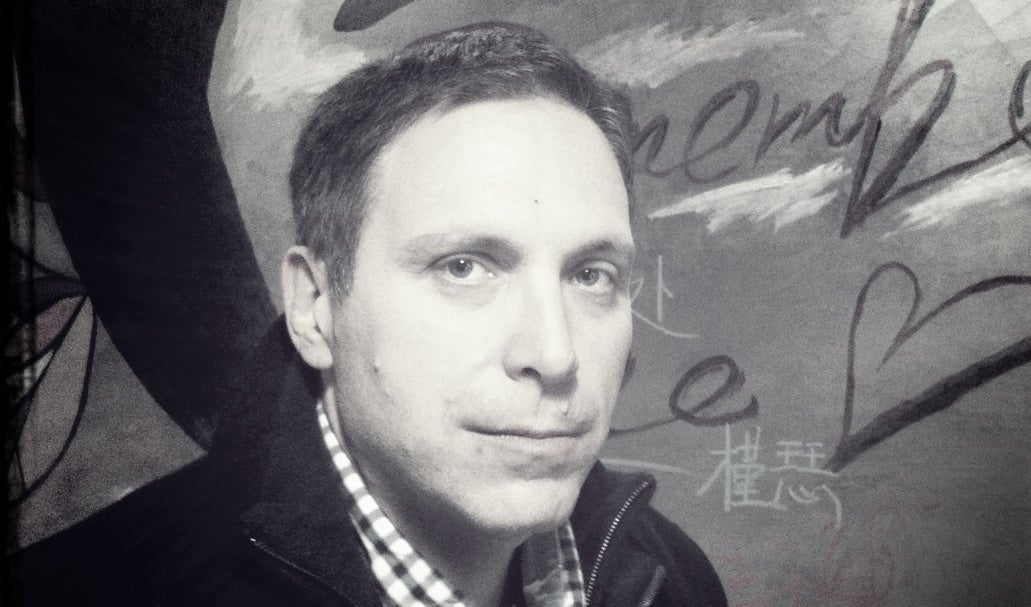
Joseph Shavit
Head Science News Writer | Communicating Innovation & Discovery
Based in Los Angeles, Joseph Shavit is an accomplished science journalist, head science news writer and co-founder at The Brighter Side of News, where he translates cutting-edge discoveries into compelling stories for a broad audience. With a strong background spanning science, business, product management, media leadership, and entrepreneurship, Joseph brings a unique perspective to science communication. His expertise allows him to uncover the intersection of technological advancements and market potential, shedding light on how groundbreaking research evolves into transformative products and industries.