Robots are safer and softer thanks to new artificial ‘muscles’
Engineers have developed a new soft, flexible device that makes robots move by expanding and contracting — just like a human muscle.
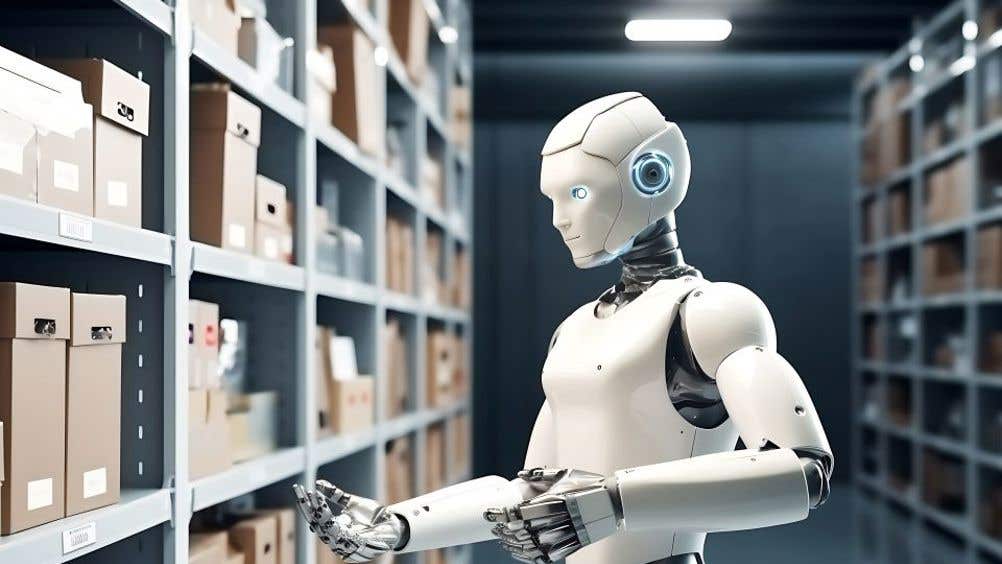
Engineers have developed a new soft, flexible device that makes robots move by expanding and contracting — just like a human muscle. (CREDIT: The Engineer)
In an impressive leap in robotics, engineers at Northwestern University have created a novel, soft, flexible device mimicking human muscle movements. This innovation is set to transform the way robots interact with their environment.
The heart of this breakthrough is an actuator—a component that enables movement. To showcase its capabilities, researchers fashioned a cylindrical, worm-like soft robot and an artificial bicep. The soft robot adeptly maneuvered through narrow, pipe-like environments, while the artificial bicep demonstrated remarkable strength by lifting a 500-gram weight 5,000 times without failure.
Constructed from a common rubber and 3D-printed, the actuator is remarkably cost-effective, with each unit costing around $3, not including the motor. This contrasts sharply with traditional rigid actuators, which can run into hundreds or even thousands of dollars. The affordability of this new actuator paves the way for developing more practical and safe robots for various applications.
Published in the journal Advanced Intelligent Systems, this research is driven by a longstanding goal among roboticists: to make robots safer and more adaptable to human-centric environments. “If a soft robot hit a person, it would not hurt nearly as much as getting hit with a rigid, hard robot,” explains Ryan Truby, who led the study. Truby, the June and Donald Brewer Junior Professor of Materials Science and Engineering at Northwestern, believes that the cost-effectiveness of these actuators could allow for broader applications previously deemed too expensive.
The research team, including Taekyoung Kim, a postdoctoral scholar, and Pranav Kaarthik, a Ph.D. candidate, aimed to design robots that move and behave like living organisms. Traditional rigid actuators, while reliable, lack flexibility and adaptability. Inspired by the simultaneous contraction and stiffening of human muscles, Truby and his team sought to replicate this dynamic in their soft actuators.
Related Stories
The journey began with 3D-printing cylindrical structures called "handed shearing auxetics" (HSAs) from rubber. HSAs are intricate and difficult to fabricate but essential for the unique movement and properties desired. Previously, the team used expensive printers and rigid plastic resins, which limited the flexibility of the HSAs.
Kim’s breakthrough came with using thermoplastic polyurethane, a rubber commonly found in cellphone cases, to print the HSAs on a standard desktop 3D printer. This made the HSAs much softer and more flexible, though it presented the challenge of how to twist them to achieve the desired movement.
Earlier versions of the soft actuator used multiple motors to twist and extend the HSAs, complicating the design and reducing softness. The goal was to drive a single HSA with one motor. Kim's solution involved adding a soft, extendable rubber bellows to the structure, acting as a rotating shaft. With the motor providing torque, the actuator could extend and contract by simply turning in one direction or the other.
“Essentially, Taekyoung engineered two rubber parts to create muscle-like movements with the turn of a motor,” Truby says. This simplified the production process significantly, making the actuator more accessible to other roboticists.
The team’s efforts culminated in a crawling soft robot, propelled by the actuator through a complex environment resembling a pipe. This robot, measuring just 26 centimeters in length, can crawl forward and backward at over 32 centimeters per minute. The actuator's unique property of stiffening when extended—akin to how human muscles stiffen to transmit force—sets it apart from previous soft actuators that typically become softer under load.
“Like a muscle, these soft actuators actually stiffen,” Truby explains, highlighting how this feature enables the robot to perform work more effectively. This characteristic is crucial for bioinspired robotics, where the ability to stiffen under load can significantly enhance performance and versatility.
The potential applications for these new actuators are vast. Robots that can move like living organisms could perform tasks conventional robots struggle with, from navigating tight spaces to handling delicate objects. This innovation could lead to safer interactions between robots and humans, especially in environments where human contact is inevitable.
Truby's research, supported by his Young Investigator Award from the Office of Naval Research and Northwestern’s Center for Engineering and Sustainability Resilience, represents a significant step towards more practical and bioinspired robotics. As the field continues to evolve, the affordability and versatility of these actuators may lead to widespread adoption, fundamentally changing how robots are designed and used.
With this development, you are witnessing a transformative moment in robotics. The journey from rigid, costly actuators to flexible, affordable, muscle-like components marks a new era where robots can safely and efficiently operate in human-centric environments. The future of robotics is not just about advanced technology but making it accessible and practical for real-world applications.
Note: Materials provided above by the The Brighter Side of News. Content may be edited for style and length.
Like these kind of feel good stories? Get the Brighter Side of News' newsletter.
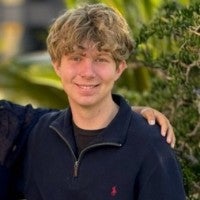
Joshua Shavit
Science & Technology Writer | AI and Robotics Reporter
Joshua Shavit is a Los Angeles-based science and technology writer with a passion for exploring the breakthroughs shaping the future. As a contributor to The Brighter Side of News, he focuses on positive and transformative advancements in AI, technology, physics, engineering, robotics and space science. Joshua is currently working towards a Bachelor of Science in Business Administration at the University of California, Berkeley. He combines his academic background with a talent for storytelling, making complex scientific discoveries engaging and accessible. His work highlights the innovators behind the ideas, bringing readers closer to the people driving progress.