Revolutionizing indoor air quality with 3D-printed geopolymer tiles
Discover how 3D-printed geopolymer tiles enhance indoor humidity control, reduce emissions, and promote sustainable construction practices.
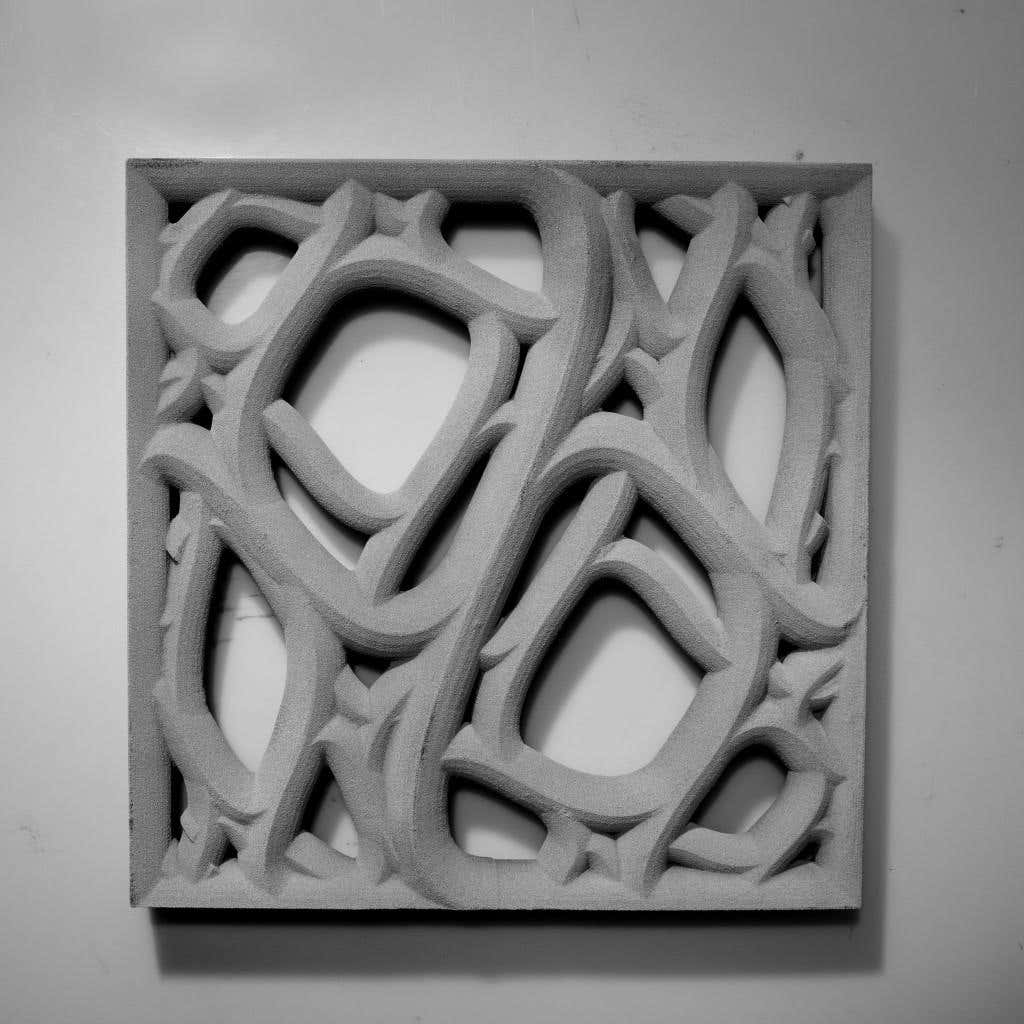
Learn how 3D-printed geopolymer tiles combine innovative design and material science to improve indoor air quality and reduce carbon emissions. (CREDIT: University of Toronto)
Controlling indoor humidity is a significant challenge in construction and building maintenance. High humidity fosters mold, allergens, and even the spread of viruses, while low humidity can dry out mucous membranes and exacerbate respiratory issues.
Conventional humidity control relies on mechanical systems that consume energy and increase carbon emissions. Emerging research highlights a sustainable alternative: 3D-printed geopolymer composites. These innovative materials promise to revolutionize indoor air quality and reduce environmental impacts.
Maintaining indoor relative humidity between 40% and 60% is essential for health and comfort. Humidity levels outside this range can lead to physical discomfort, exacerbate respiratory and rheumatic conditions, and promote the survival of viruses like SARS-CoV-2.
This ideal range minimizes bacterial growth, limits mold and dust mites, and supports better respiratory health. Despite its importance, many indoor environments struggle to maintain these conditions consistently, especially in regions with fluctuating climates.
Conventional systems such as dehumidifiers and air conditioning often consume significant energy, contributing to greenhouse gas emissions. For instance, dehumidification during cooling seasons can account for up to 40% of energy used in air conditioning.
To address this issue, researchers are developing passive solutions to regulate indoor moisture more sustainably. These methods not only reduce energy consumption but also offer long-term environmental benefits.
Porous, hygroscopic building materials offer a compelling alternative. These materials absorb excess moisture when humidity rises and release it when the air becomes dry. Such properties make them ideal for spaces like bedrooms, offices, and public areas that experience fluctuating moisture levels due to human activity. Geopolymer composites, made from industrial waste and natural materials, are leading this charge.
Geopolymers, first introduced in the 1970s, are materials derived from aluminosilicate precursors activated by alkaline solutions. Their production emits significantly less CO2 than traditional cement, especially when incorporating industrial byproducts like quarry waste. Geopolymers are durable, resistant to harsh environmental conditions, and free of volatile organic compounds.
Published in the journal, Nature Communications, recent innovations in 3D printing have further unlocked the potential of geopolymers.
Using binder jetting technology, researchers have created porous materials optimized for moisture buffering. This method layers a mixture of aggregates and geopolymer precursors, selectively binding them with an activator solution. The unbound powder supports overhangs and can be reused in future prints, reducing waste.
Related Stories
Binder jetting offers unique advantages over traditional extrusion methods, particularly for complex geometries. For example, gyroid-shaped designs maximize surface area while minimizing material use, resulting in lighter components with excellent functionality.
A team at ETH Zurich demonstrated the efficiency of this approach by producing 4-centimeter-thick, gyroid-shaped tiles with a high surface area-to-volume ratio. These tiles use 60% less material than solid alternatives, lowering their embodied carbon footprint.
The moisture buffering value (MBV) of these 3D-printed components exceeds 14 g·m⁻²·%RH⁻¹, four times higher than conventional materials classified as “excellent” for moisture regulation. By integrating cutting-edge materials science with advanced manufacturing techniques, these tiles set a new benchmark for sustainable construction.
Laboratory tests reveal that 3D-printed geopolymer composites outperform common finishing materials like lime-cement and earthen plasters in moisture buffering and thermal performance. The materials’ high capillary water absorption and low resistance to water vapor diffusion make them ideal for managing indoor humidity.
While the thermal conductivity of these composites is slightly higher than some insulating materials, their ability to absorb and release moisture sets them apart. These materials can store significant moisture during humidity spikes and release it as conditions normalize, ensuring a stable indoor environment.
Dynamic simulations show the practical benefits of these materials in real-world scenarios. For instance, a public library in Oporto, Portugal, was modeled with walls and ceilings lined with 3D-printed geopolymer tiles.
The results indicated an 85% improvement in annual hygrometric comfort compared to conventional materials. Such applications demonstrate the potential for geopolymer tiles to transform spaces where humidity control is critical, from offices to public facilities.
The ability to passively regulate humidity is particularly valuable in high-traffic areas, where mechanical systems often struggle to keep up with fluctuating moisture levels. These materials can absorb excess humidity during peak occupancy and release it during off-hours, maintaining comfort without increasing energy consumption.
This passive regulation is especially beneficial in spaces like museums, libraries, and government offices, where preserving indoor air quality is essential for both occupants and sensitive materials.
The environmental advantages of geopolymer composites extend beyond their humidity-regulating properties. By repurposing industrial byproducts like marble quarry waste, these materials support circular economy principles. The production process requires lower temperatures than traditional cement manufacturing, reducing energy consumption and CO2 emissions.
The ETH Zurich study compared the environmental impact of these tiles to mechanical dehumidification systems. Over a 30-year lifecycle, the tiles emitted significantly less greenhouse gas while providing comparable humidity control.
Even when compared to traditional clay plaster, geopolymer tiles offered greater moisture storage capacity, albeit with slightly higher emissions. These findings underscore the importance of optimizing material design for sustainability.
To further reduce the carbon footprint of these materials, researchers are exploring alternative formulations and activators. Collaborations with institutions like Aalto University and Turin Polytechnic aim to refine the geopolymer composition and enhance the efficiency of the 3D printing process.
Advances in binder jetting technology are also expected to expand the range of shapes and applications, making this innovation accessible for a broader array of building projects.
As the construction industry moves toward net-zero emissions by 2050, innovations like 3D-printed geopolymer composites will play a crucial role. These materials not only address pressing issues like indoor air quality but also align with global efforts to mitigate climate change. Their ability to passively regulate humidity, coupled with their low environmental impact, makes them a promising solution for future buildings.
In addition to improving indoor air quality, these materials can significantly reduce energy consumption associated with mechanical systems. By integrating moisture-buffering components into building designs, architects and engineers can create environments that are both comfortable and sustainable. The use of waste materials like marble quarry byproducts further highlights the potential for these technologies to support circular economy practices.
From public libraries to high-traffic office spaces, 3D-printed geopolymer tiles offer a vision of healthier, more sustainable indoor environments.
By merging cutting-edge material science with advanced manufacturing techniques, this technology sets a new standard for the built environment. The journey to widespread adoption may still be underway, but the potential for transformative impact is already clear.
The research at ETH Zurich has shown that combining geopolymer technology with 3D printing can produce wall and ceiling components for efficient moisture buffering. These components offer a scalable solution for reducing energy use and enhancing indoor comfort.
As further advancements are made, the construction industry will likely see broader applications of this innovative approach.
Note: Materials provided above by The Brighter Side of News. Content may be edited for style and length.
Like these kind of feel good stories? Get The Brighter Side of News' newsletter.
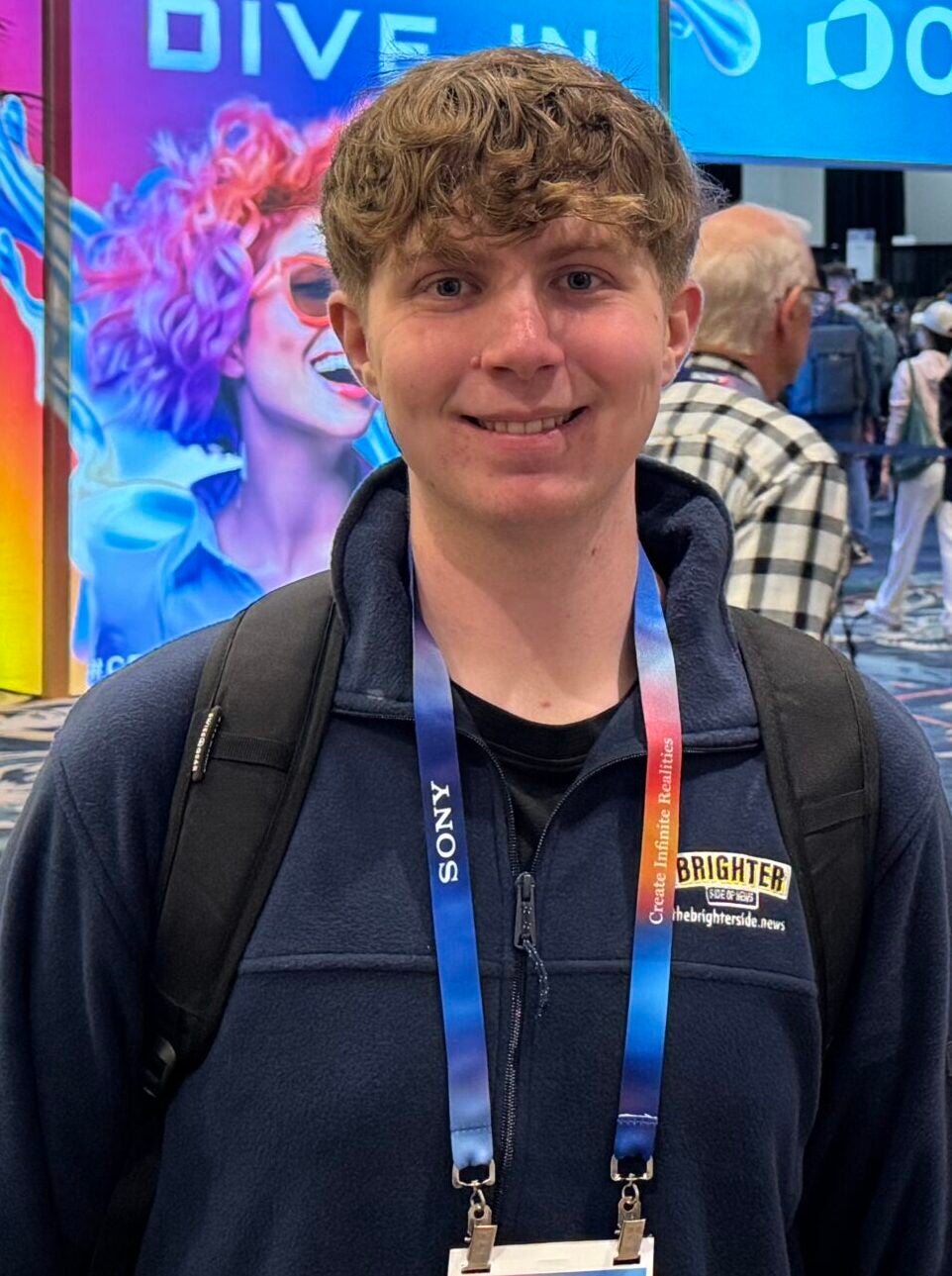
Joshua Shavit
Science & Technology Writer | AI and Robotics Reporter
Joshua Shavit is a Los Angeles-based science and technology writer with a passion for exploring the breakthroughs shaping the future. As a contributor to The Brighter Side of News, he focuses on positive and transformative advancements in AI, technology, physics, engineering, robotics and space science. Joshua is currently working towards a Bachelor of Science in Business Administration at the University of California, Berkeley. He combines his academic background with a talent for storytelling, making complex scientific discoveries engaging and accessible. His work highlights the innovators behind the ideas, bringing readers closer to the people driving progress.