New 3D printing process creates recyclable plastics that stretch and flex
Princeton engineers developed scalable 3D printing for affordable, recyclable soft plastics with customizable properties, ideal for robotics and devices
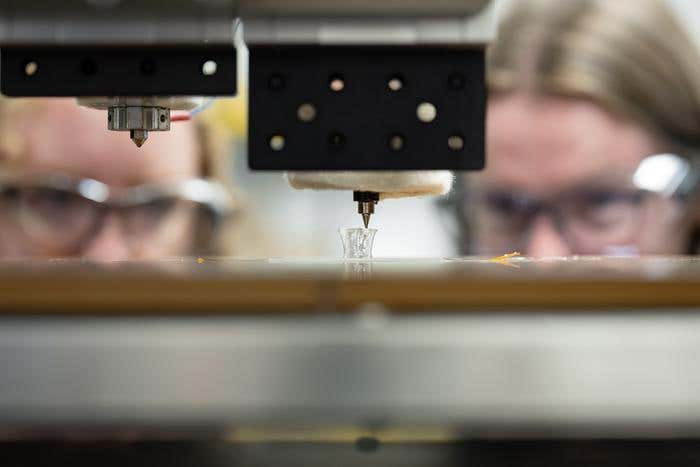
Discover how a novel 3D printing method enables recyclable, affordable soft plastics with tailored properties, promising advancements in robotics and healthcare. (CREDIT: Sameer A. Khan/Fotobuddy)
Nature often demonstrates extraordinary ingenuity in material design, where structure dictates function. Examples include the toughness of nacre, the rigidity of bamboo, and the vivid coloration in butterfly wings. These properties arise from hierarchical, self-assembled structures.
However, synthetic materials rarely achieve this level of structural sophistication—especially in soft materials. Recent advances in 3D printing, specifically high operating temperature direct ink writing (HOT-DIW), are now poised to change that landscape.
Researchers at Princeton University have developed a scalable 3D printing technique to create highly customizable and recyclable soft plastics. Published in the journal, Advanced Functional Materials, this innovation uses thermoplastic elastomers (TPEs), a class of widely available, nanostructured polymers, to fabricate materials with programmable mechanical properties.
Emily Davidson, assistant professor of chemical and biological engineering, explained, “We can create materials that have tailored properties in different directions.” This breakthrough enables engineers to print devices that stretch and flex in specific directions while maintaining rigidity in others. The approach has transformative potential for applications in soft robotics, medical devices, and high-performance athletic gear.
The secret lies in TPEs’ unique molecular architecture. These block copolymers consist of stiff cylindrical structures embedded in a flexible polymer matrix. At just 5-7 nanometers thick, these cylinders are oriented during the printing process, creating a material that is strong in one direction and soft in others. This directional control enables engineers to design products with specific mechanical responses in different regions.
The researchers used HOT-DIW to induce alignment of TPE nanostructures during the printing process. This technique applies controlled shear and extensional flows to align the stiff nanocylinders along programmable print paths. By carefully selecting the printing parameters, the team achieved high structural and mechanical anisotropy—up to 85 times difference in tensile modulus between aligned and non-aligned directions.
Thermal annealing, a controlled heating and cooling process, proved critical to enhancing material performance. Alice Fergerson, a graduate student and lead author on the study, emphasized the importance of annealing. “It both drastically improves the properties after printing, and it allows the things we print to be reusable many times and even self-heal if the item gets damaged or broken.”
Related Stories
By annealing the printed structures, the researchers improved the order and alignment of nanostructures, resulting in enhanced mechanical properties. Additionally, annealing enabled self-healing capabilities, where damaged components could be repaired with no loss in functionality. In tests, a cut sample of the printed plastic was rejoined through annealing, demonstrating performance indistinguishable from the original material.
One of the standout features of this technique is its affordability. Traditional liquid crystal elastomers (LCEs), which also offer tunable mechanical properties, are prohibitively expensive at approximately $2.50 per gram and require complex multi-stage processing. In contrast, TPEs cost about $0.01 per gram and can be processed with commercial 3D printers.
Davidson’s team demonstrated that their process is scalable for industrial applications, offering a low-cost solution for manufacturing soft, architected materials. The intrinsic recyclability of TPEs further enhances their appeal. Unlike chemically cross-linked elastomers, TPEs can be reprocessed through melting without degradation, making them an environmentally friendly choice for large-scale production.
The team’s ability to incorporate functional additives into TPEs without compromising their mechanical properties is another significant advancement. For example, they integrated an organic molecule that causes the plastic to glow red under ultraviolet light. This feature could expand the material’s applications into areas like wearables and sensors.
This innovative approach to 3D printing soft materials holds promise across multiple fields. Soft robotics could benefit from materials that combine flexibility with strength, enabling more adaptable and durable designs. Medical devices and prosthetics could be tailored to meet individual patient needs, while athletic gear like helmets and shoe soles could achieve unprecedented performance.
“The elastomer we are using forms nanostructures that we are able to control,” Davidson noted. This control opens the door to highly specialized designs. For instance, the team demonstrated their printer’s versatility by creating complex structures such as a tiny plastic vase and printed text spelling “Princeton” with sharp turns. These examples illustrate the precision and adaptability of the technique.
Future work will explore new printable architectures compatible with wearable electronics and biomedical devices. The researchers also plan to investigate the integration of additional functionalities, such as sensors and conductive materials, to further expand the utility of TPE-based structures.
This study showcases the potential for combining scientific insight into polymer behavior with advanced manufacturing techniques. By aligning nanoscale structures through 3D printing, Davidson’s team has achieved a rare combination of affordability, customizability, and sustainability.
As industries continue to seek greener and more efficient manufacturing methods, innovations like these could set new standards for material design. With its ability to create robust, recyclable, and precisely engineered materials, this breakthrough promises to reshape industries ranging from healthcare to consumer products.
Note: Materials provided above by The Brighter Side of News. Content may be edited for style and length.
Like these kind of feel good stories? Get The Brighter Side of News' newsletter.
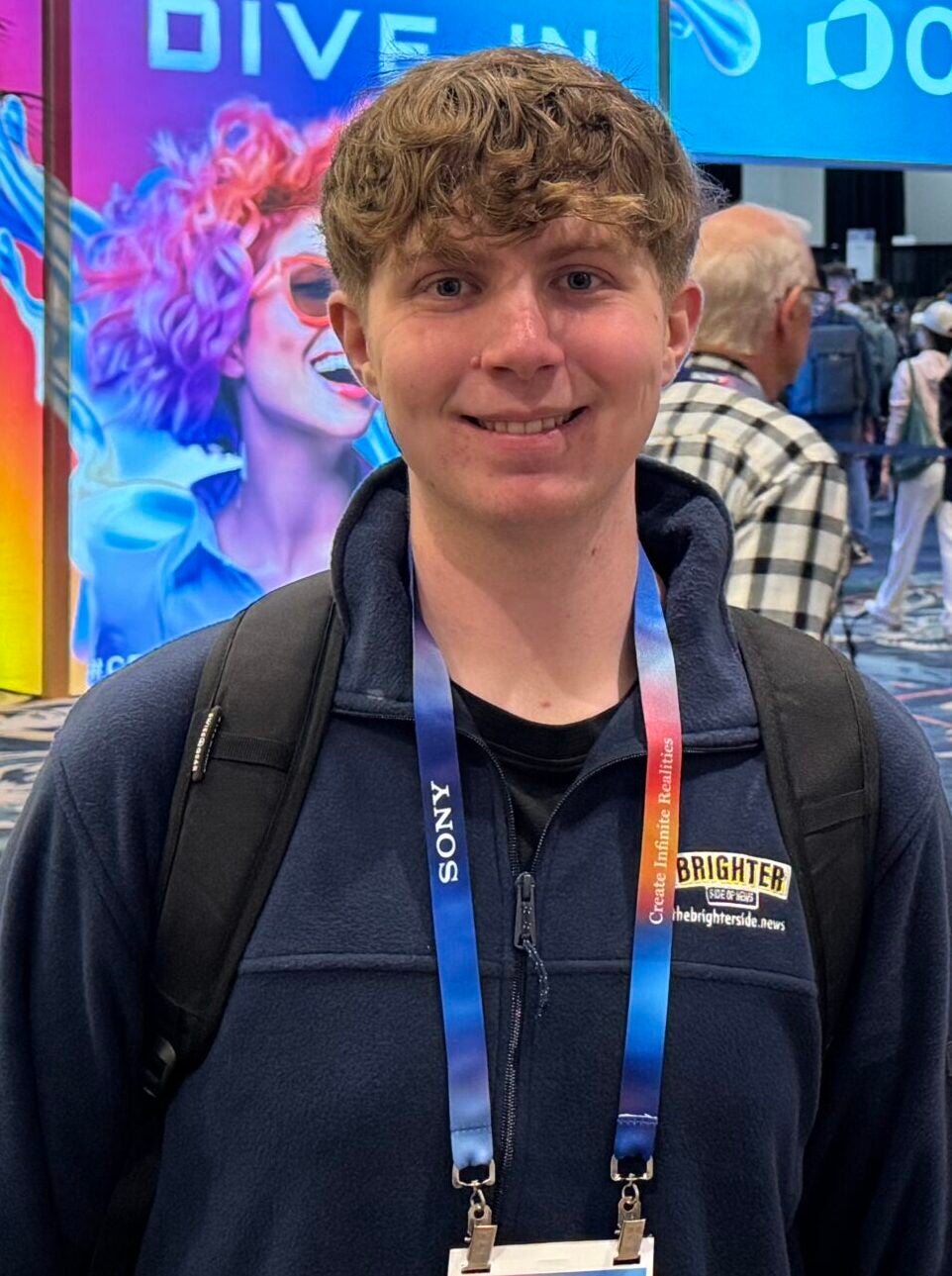
Joshua Shavit
Science & Technology Writer | AI and Robotics Reporter
Joshua Shavit is a Los Angeles-based science and technology writer with a passion for exploring the breakthroughs shaping the future. As a contributor to The Brighter Side of News, he focuses on positive and transformative advancements in AI, technology, physics, engineering, robotics and space science. Joshua is currently working towards a Bachelor of Science in Business Administration at the University of California, Berkeley. He combines his academic background with a talent for storytelling, making complex scientific discoveries engaging and accessible. His work highlights the innovators behind the ideas, bringing readers closer to the people driving progress.