Groundbreaking titanium alloy “Metamaterial” revolutionizes aerospace technologies
A groundbreaking metamaterial engineered with unique electromagnetic properties has been developed from a commonly used titanium alloy
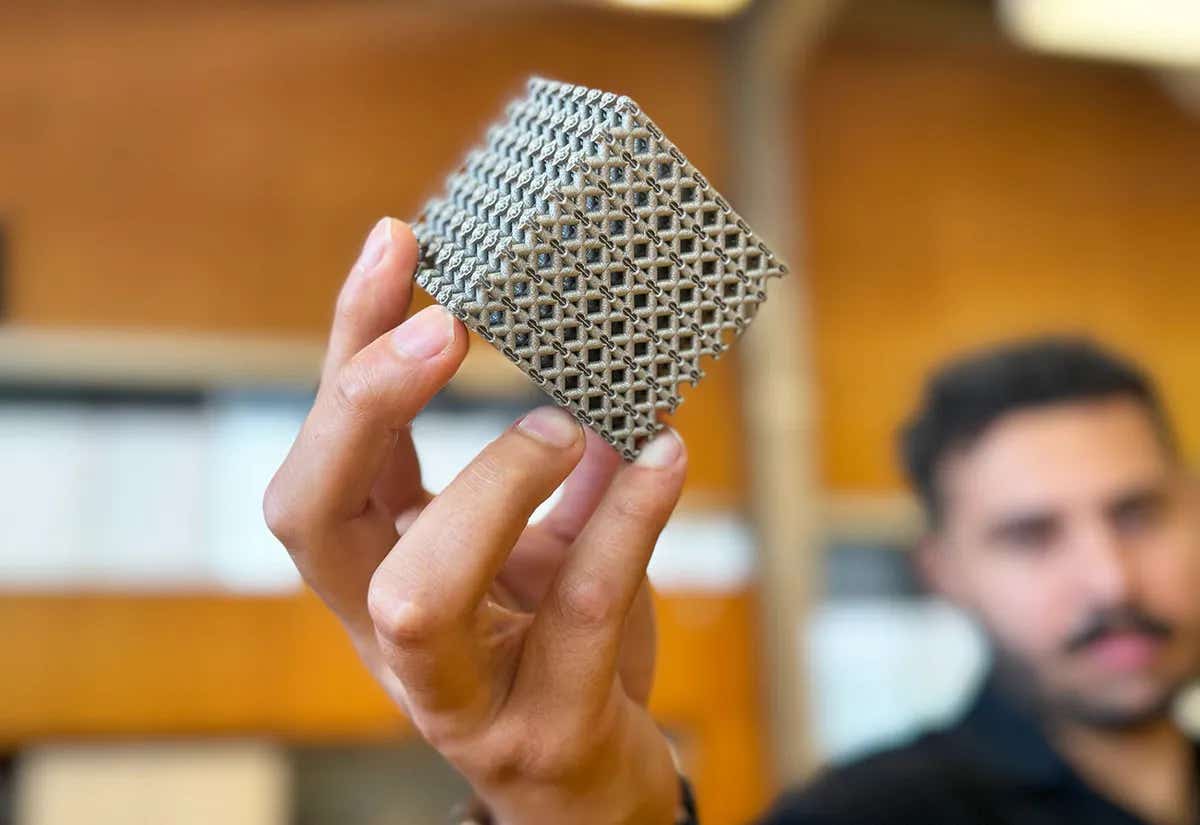
A groundbreaking metamaterial engineered with unique electromagnetic properties not found in nature, has been developed from a commonly used titanium alloy. PhD candidate Jordan Noronha holding a sample of the new titanium lattice structure 3D printed in cube form. (CREDIT: RMIT)
A groundbreaking metamaterial engineered with unique electromagnetic properties not found in nature, has been developed from a commonly used titanium alloy.
Despite its conventional origin, this material boasts exceptional strength due to its innovative lattice structure, surpassing existing alloys in aerospace applications by 50 percent.
Inspired by the robustness of natural structures like Victoria water lilies and organ-pipe corals, researchers sought to replicate their strength and lightness. Historically, mimicking such cellular structures in artificial materials has proven challenging due to manufacturing constraints and uneven load distribution.
Distinguished Professor Ma Qian highlighted this issue, noting that conventional cellular materials often distribute stress unevenly, weakening the structure. However, leveraging advancements in metal 3D printing, the team devised a novel lattice design that evenly disperses stress, mitigating weak points.
Related Stories
"We designed a hollow tubular lattice structure with a reinforcing band, combining strength and lightness in a previously unseen manner," explained Qian. "This innovative approach merges complementary lattice structures to distribute stress uniformly, avoiding common weak points."
Utilizing laser powder bed fusion at RMIT's Advanced Manufacturing Precinct, the team successfully fabricated titanium lattice cubes stronger than the industry-standard cast magnesium alloy WE54. This advancement effectively reduces stress concentration on the lattice's weak spots, enhancing its resilience against cracks.
Moreover, the double lattice design deflects potential cracks, preserving the material's toughness. This scalable structure can vary in size from millimeters to meters using different printing methods, offering versatility in manufacturing applications.
Compression testing shows (left) stress concentrations in red and yellow on the hollow strut lattice, while (right) the double lattice structure spreads stress more evenly to avoid hot spots. (CREDIT: RMIT)
Lead author Jordan Noronha emphasized the material's superior strength and resistance to permanent shape change compared to existing alloys. Despite its current temperature limit of 350°C (662°F), the team aims to enhance its capabilities to withstand temperatures up to 600°C (1,112°F), making it ideal for aerospace and firefighting drones.
However, widespread adoption may be hindered by the limited availability of the technology required for fabrication. Noronha acknowledged that traditional manufacturing methods are impractical for intricate metal metamaterials, but expressed optimism about future accessibility and efficiency improvements in metal 3D printing.
Professor Martin Leary, Professor Ma Qian, Jordan Noronha and Professor Milan Brandt at RMIT's Centre for Additive Manufacturing. (CREDIT: RMIT)
"As technology advances, metal 3D printing will become more accessible, facilitating faster production and broader implementation of our high-strength metamaterials," Noronha stated. "This enables easy fabrication of complex components for various applications."
While further refinement and technological advancements are needed for widespread adoption, its potential impact on various industries, particularly aerospace and manufacturing, is promising.
Technical Director of RMIT's Advanced Manufacturing Precinct, Distinguished Professor Milan Brandt, said the team welcomed companies wanting to collaborate on the many potential applications.
“Our approach is to identify challenges and create opportunities through collaborative design, knowledge exchange, work-based learning, critical problem-solving and translation of research,” he said.
The study, ‘Titanium Multi-Topology Metamaterials with Exceptional Strength’, was published in Advanced Materials.
Note: Materials provided above by The Brighter Side of News. Content may be edited for style and length.
Like these kind of feel good stories? Get the Brighter Side of News' newsletter.
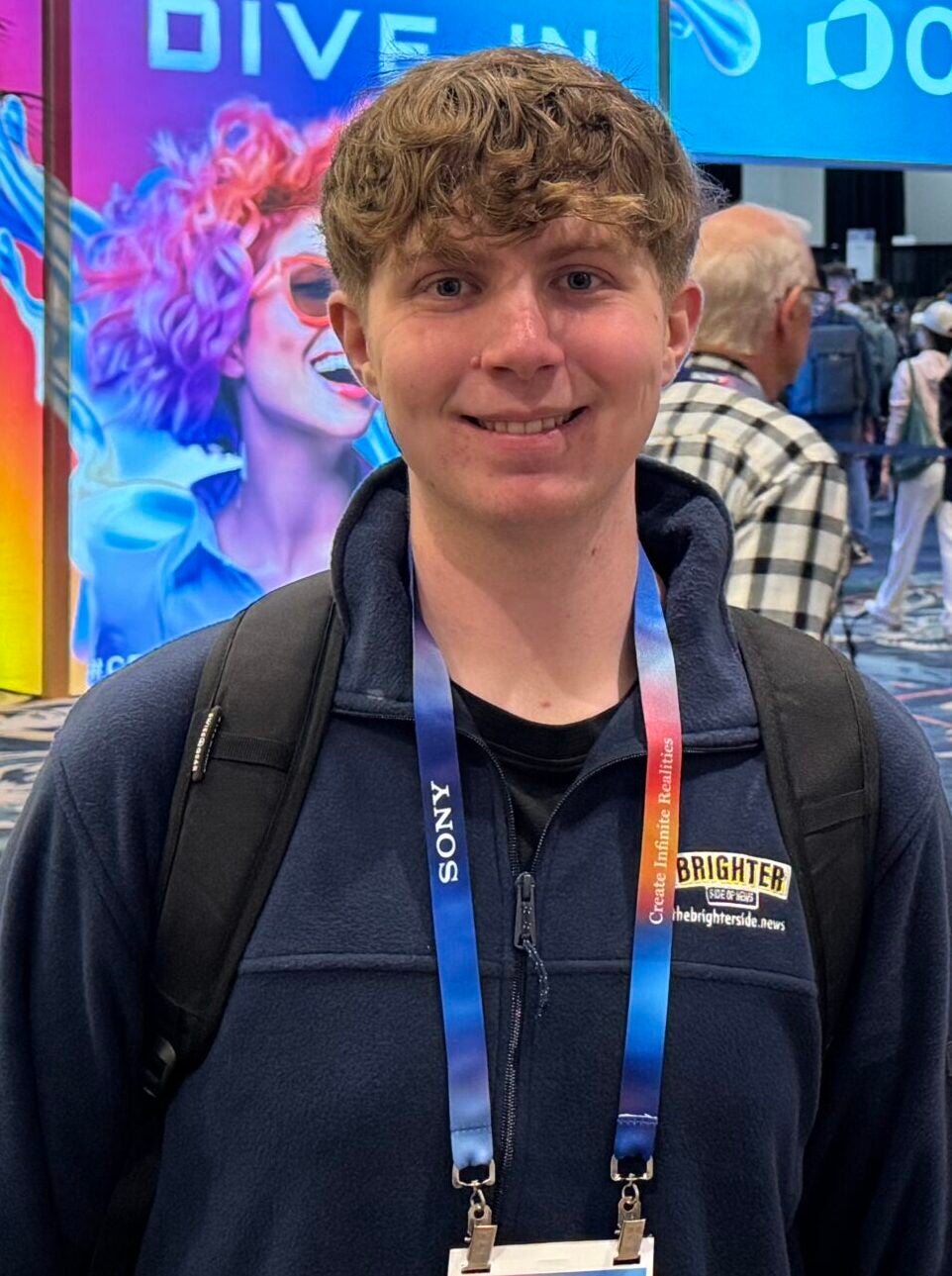
Joshua Shavit
Science & Technology Writer | AI and Robotics Reporter
Joshua Shavit is a Los Angeles-based science and technology writer with a passion for exploring the breakthroughs shaping the future. As a contributor to The Brighter Side of News, he focuses on positive and transformative advancements in AI, technology, physics, engineering, robotics and space science. Joshua is currently working towards a Bachelor of Science in Business Administration at the University of California, Berkeley. He combines his academic background with a talent for storytelling, making complex scientific discoveries engaging and accessible. His work highlights the innovators behind the ideas, bringing readers closer to the people driving progress.