Groundbreaking new electric reactor reaches incredible 85% efficiency
Industrial processes in the US contribute to about one-third of the nation’s CO2 emissions—outpacing cars, trucks, and airplanes combined.
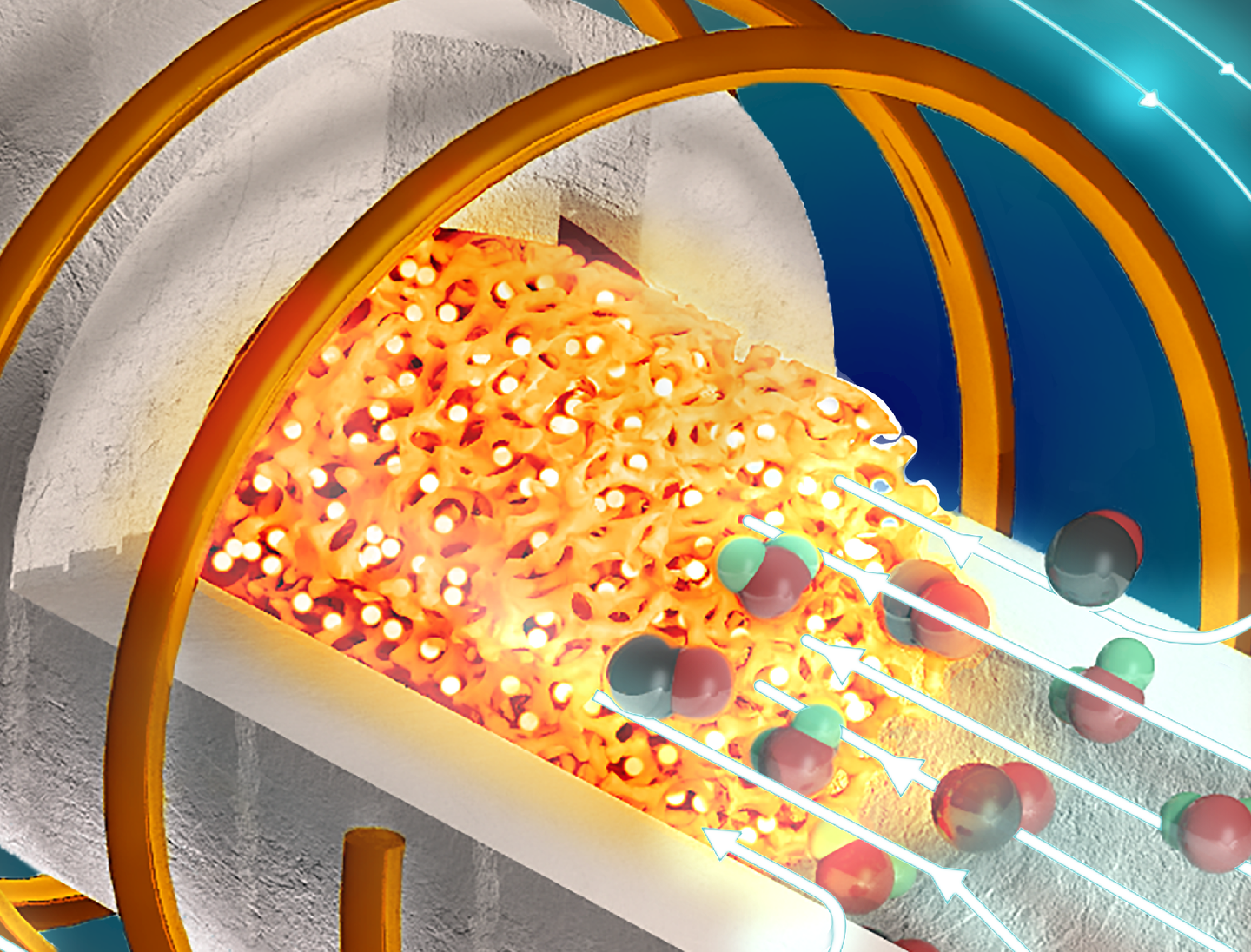
This image depicts the inductively heated metamaterial reactor with catalysts filling the ceramic foam baffle. It is producing carbon monoxide and water from the reverse water gas shift reaction. (CREDIT: Dolly Mantle)
Industrial processes in the United States contribute to about one-third of the nation's carbon dioxide emissions—outpacing even the annual emissions from passenger vehicles, trucks, and airplanes combined. Addressing this significant source of greenhouse gases is crucial in mitigating climate change, but it's a complex challenge.
A team of researchers at Stanford Engineering has developed a groundbreaking thermochemical reactor that could play a key role in reducing these emissions. This innovative reactor generates the high temperatures needed for many industrial processes using electricity rather than burning fossil fuels.
According to their findings, published in the journal Joule, this new reactor design is not only more efficient but also smaller and cheaper than current fossil fuel-based technology.
Jonathan Fan, an associate professor of electrical engineering at Stanford and the senior author of the paper, emphasized the significance of this development. “We have an electrified and scalable reactor infrastructure for thermochemical processes that features ideal heating and heat-transfer properties,” he explained. “Essentially, we’re pushing reactor performance to its physical limits, and we’re using green electricity to power it.”
The conventional thermochemical reactors operate by burning fossil fuels to heat a fluid, which then transfers heat through pipes within the reactor. This process is similar to how a boiler sends hot water to radiators in a building, but on a much larger scale and at much higher temperatures. However, this method is energy-intensive, requiring extensive infrastructure, and it has significant heat loss potential at various stages.
The new reactor, however, uses magnetic induction to generate heat—a process similar to that used in induction stoves. Instead of relying on external heating and transferring that heat through pipes, induction heating creates heat directly within the reactor. This is achieved by harnessing the interaction between electric currents and magnetic fields.
For example, if you wrap a wire around a steel rod and run an alternating current through the coil, the resulting magnetic field induces a current in the steel. Due to steel's imperfect conductivity, some of this current converts to heat, effectively heating the entire steel piece from within, rather than from the outside.
Related Stories
While this method might sound straightforward, adapting it for industrial use presents unique challenges. Industrial reactors need to evenly distribute heat in a three-dimensional space and must be far more efficient than a household stovetop. To achieve this, the Stanford team used high-frequency currents, which alternate rapidly, combined with reactor materials that are poor conductors of electricity.
These high-frequency currents were made possible by new, high-efficiency electronics developed by Juan Rivas-Davila, an associate professor of electrical engineering at Stanford and a co-author of the paper. These currents were then used to inductively heat a three-dimensional lattice made from a poorly conducting ceramic material at the core of the reactor.
The lattice structure is crucial because it artificially reduces electrical conductivity even further. Moreover, the voids in the lattice can be filled with catalysts—materials that need to be heated to initiate chemical reactions. This setup not only enhances heat transfer but also allows the reactor to be much smaller than traditional fossil fuel reactors.
“You’re heating a large surface area structure that is right next to the catalyst, so the heat you’re generating gets to the catalyst very quickly to drive the chemical reactions,” Fan explained. “Plus, it’s simplifying everything. You’re not transferring heat from somewhere else and losing some along the way, you don’t have any pipes going in and out of the reactor—you can fully insulate it. This is ideal from an energy management and cost point of view.”
In their proof-of-concept demonstration, the researchers used this reactor to power the reverse water gas shift reaction—a chemical process that requires high heat and can turn captured carbon dioxide into a valuable gas used to create sustainable fuels. They employed a new sustainable catalyst developed by Matthew Kanan, a professor of chemistry at Stanford and a co-author of the paper.
The reactor demonstrated an efficiency of over 85%, meaning it converted nearly all the electrical energy into usable heat. It also created ideal conditions for the chemical reaction, with carbon dioxide being converted at the theoretically predicted rate—a significant achievement, as new reactor designs often fall short of theoretical predictions.
“As we make these reactors even larger or operate them at even higher temperatures, they just get more efficient,” Fan said. “That’s the story of electrification—we’re not just trying to replace what we have, we’re creating even better performance.”
Looking ahead, Fan, Rivas-Davila, Kanan, and their colleagues are focused on scaling up their reactor technology and expanding its applications. They are working to adapt this technology for capturing carbon dioxide and manufacturing cement, two industries with high carbon footprints.
Additionally, they are collaborating with industrial partners in the oil and gas sectors to explore what it would take for these industries to adopt this technology. Economic analyses are also underway to understand how to make these sustainable solutions more affordable and widespread.
“Electrification affords us the opportunity to reinvent infrastructure, breaking through existing bottlenecks and shrinking and simplifying these types of reactors, in addition to decarbonizing them,” Fan said. “Industrial decarbonization is going to require new, systems-level approaches, and I think we’re just getting started.”
The development of this new reactor could be a pivotal step toward reducing the carbon emissions of industrial processes, ultimately helping to safeguard the climate for future generations.
Note: Materials provided above by The Brighter Side of News. Content may be edited for style and length.
Like these kind of feel good stories? Get The Brighter Side of News' newsletter.
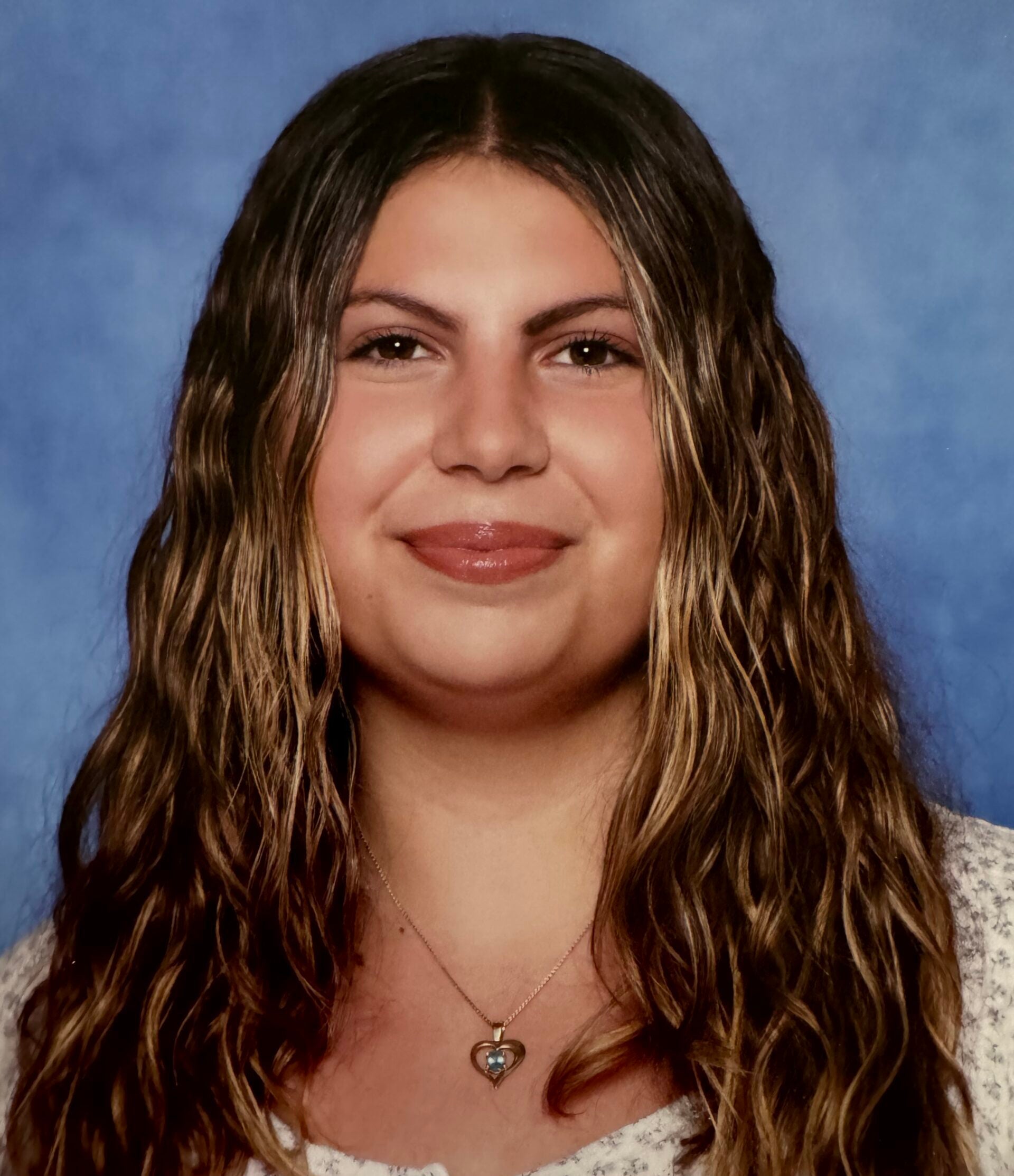
Rebecca Shavit
Science & Technology Journalist | Innovation Storyteller
Based in Los Angeles, Rebecca Shavit is a dedicated science and technology journalist who writes for The Brighter Side of News, an online publication committed to highlighting positive and transformative stories from around the world. With a passion for uncovering groundbreaking discoveries and innovations, she brings to light the scientific advancements shaping a better future. Her reporting spans a wide range of topics, from cutting-edge medical breakthroughs and artificial intelligence to green technology and space exploration. With a keen ability to translate complex concepts into engaging and accessible stories, she makes science and innovation relatable to a broad audience.