Cutting-edge new technology safely recycles 99% of used solar panels
Startup is tackling a major global challenge: recycling the millions of solar panels expected to reach the end of their useful lives by 2050
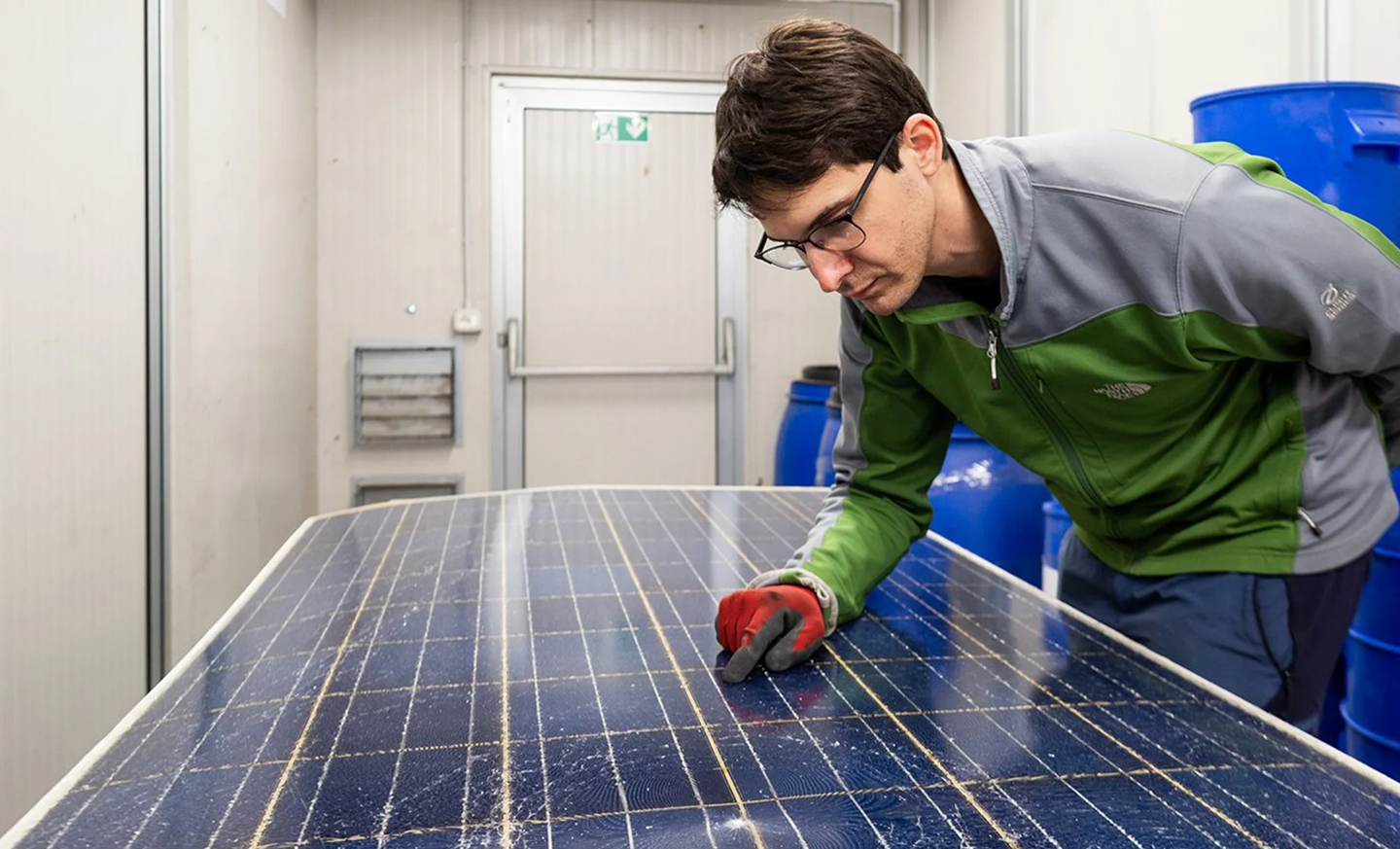
The world’s reliance on solar energy is rapidly growing, with over 1.2 terawatts of solar power already deployed globally. (CREDIT: 9-Tech)
In the heart of Venice’s industrial area, a small startup is tackling a significant global challenge: recycling the millions of solar panels expected to reach the end of their useful lives by 2050. The startup, 9-Tech, is addressing this issue head-on, working within the confines of a modified shipping container at the Green Propulsion Laboratory in the Marghera port.
The world’s reliance on solar energy is rapidly growing, with over 1.2 terawatts of solar power already deployed globally. Solar panel installation is accelerating, currently exceeding 400 gigawatts annually, and is projected to surge to 3 terawatts per year by 2030, according to research from the National Renewable Energy Laboratory (NREL). This growing deployment means that the need for effective recycling methods will become increasingly urgent.
Recycling solar panels is no small feat. These panels are built to withstand harsh environmental conditions for 20 to 30 years, and even after decades in the sun, they remain difficult to dismantle. Most recycling facilities only manage to salvage the aluminum frames and glass panes, discarding the more valuable but less accessible materials like silicon, silver, and copper.
In response, researchers worldwide are pursuing advanced recycling techniques. The most effective methods proposed can recover up to 90% of the valuable materials in a crystalline silicon photovoltaic (PV) module. However, these processes are expensive and often involve hazardous chemicals, making them less viable on a large scale.
According to Garvin Heath, principal environmental engineer at NREL, no current recycling method is as cost-effective as landfilling, and very few operate at an industrial scale.
9-Tech believes it has a solution. The startup's process is unique, combining a combustion furnace, an ultrasound bath, and mechanical sorting, all within their compact testing facility. Their method, which they’ve been refining for nearly two years, avoids toxic chemicals, emits no pollutants, and recovers up to 90% of a solar panel’s materials, says Francesco Miserocchi, 9-Tech's chief technology officer.
Their approach is specifically tailored to crystalline silicon solar panels, which dominate the global market. These panels are complex, consisting of silicon wafers doped with boron and phosphorus, silver conductors screen-printed onto the wafer surface, and copper conductors soldered onto the array in a grid pattern. The entire structure is laminated in adhesive polymers, encased in tempered glass, framed in aluminum, and sealed to protect against moisture and damage.
Related Stories
One of the biggest challenges in recycling these panels is dealing with the polymers, which adhere tightly to the materials. Heath points out that removing these polymers is no small task, as they cover large surface areas and stick tenaciously.
Burning them off is an option, but it releases harmful pollutants like carbon monoxide and hydrofluoric acid. Moreover, separating the silver conductors, applied in a thin layer to the silicon, often requires toxic reagents like hydrofluoric acid or nitric acid.
9-Tech tackles these challenges innovatively. They use ultrasound to recover silver, avoiding the need for toxic chemicals. Although they do burn the polymers, they have designed a system to capture and filter out the emitted pollutants.
The process begins with workers manually removing the aluminum frame, junction box, and tempered glass from the solar panel, leaving a flexible sandwich of polymers, silicon wafers, and metal conductors. Without the structural support of the frame or glass, the sandwich bends, causing the fragile silicon to shatter.
Workers then break the tempered glass, and the remaining materials, held together by the polymers, are fed into a continuous combustion furnace. Heated to over 400°C, the polymers vaporize, and a filter captures the pollutants. The system also captures and recycles the heat from the furnace, enhancing energy efficiency.
As the materials exit the furnace, a roller strips out the copper mechanically. Sieves sort the fragments of glass and silicon by thickness. The silicon pieces, still embedded with silver, are then immersed in an organic acid bath and treated with ultrasound, which helps separate the silver from the silicon.
The ultrasound works by generating sound waves that create alternating high- and low-pressure cycles, forming cavitation bubbles that mechanically interact with the materials, loosening the bonds between them, as explained by Pietrogiovanni Cerchier, 9-Tech's CEO.
After the ultrasound bath, workers retrieve the silicon fragments with a mesh net, leaving behind a fine silver dust in the solution. This dust can be recovered through filtration or centrifugation. Overall, Cerchier claims that their pilot plant can recover 90% of the silver, 95% of the silicon, and over 99% of the copper, aluminum, and glass from a PV module. Moreover, the recovered materials are of high purity, making them suitable for various applications.
While 9-Tech's recycling process is currently more expensive than traditional methods that only recover aluminum and glass, Miserocchi believes the extraction of high-purity silicon, silver, and copper will offset these costs. He notes that this process is also more efficient than mining for virgin materials.
For instance, you can recover about 500 grams of silver from a ton of solar panels, compared to only 165 grams from a ton of ore. "A photovoltaic panel at the end of its life still has a lot to give," Miserocchi says, likening it to a "small mine of precious elements."
The startup's pilot plant currently processes about seven modules a day. However, the team plans to scale up by building a larger demonstration facility within the next 18 months, which will be capable of handling up to 800 solar modules daily. This facility will be located in the same industrial district of Venice as their current operation.
9-Tech’s method is one of many being developed worldwide to recycle crystalline silicon PV panels. A comprehensive review published in the Journal of Cleaner Production identified numerous other approaches, including thermal, chemical, mechanical, and optical methods. These techniques range from grinding the materials into small pieces and separating them by density to using laser irradiation, high-voltage pulses, and pyrolysis.
Regulations, especially in the European Union, are driving innovation in this area. Since 2012, EU rules have required PV panel manufacturers to either run their own recycling programs or partner with other schemes. Consequently, Germany, which has the most solar power capacity in Europe, also boasts one of the largest PV recycling systems globally.
However, recycling solar panels remains a high-volume business, and without catastrophic events that destroy solar power stations, spent modules arrive at recycling facilities in a slow trickle. Additionally, developing a robust supply chain for the recovered materials is still a work in progress.
Some companies, like First Solar, have taken significant steps to address these challenges. The global PV manufacturer, based in Tempe, Arizona, has established an in-house recycling program with seven facilities across five countries.
Their cadmium telluride thin-film solar panels come with a built-in recycling fee, allowing customers to send the panels back to First Solar for processing into new products. The company claims that the semiconductor material in their panels can be recycled up to 41 times, giving it a lifespan of over 1,200 years.
The difficulties associated with recycling have also inspired researchers to rethink how solar panels are manufactured. Some manufacturers are working to reduce or eliminate the use of difficult-to-recover materials like silver, replacing it with other conductive metals.
For instance, a team at NREL has demonstrated a method to eliminate polymers in PV panels by laser welding the glass panes instead, which could better protect against moisture. This technique might be particularly useful for perovskite solar modules, a promising technology that is highly susceptible to moisture and corrosion.
Recycling, however, should not be the sole focus. As Heath suggests, it’s crucial to consider alternative strategies, such as repairing or repurposing solar panels to extend their lifespan before resorting to recycling.
Note: Materials provided above by The Brighter Side of News. Content may be edited for style and length.
Like these kind of feel good stories? Get The Brighter Side of News' newsletter.
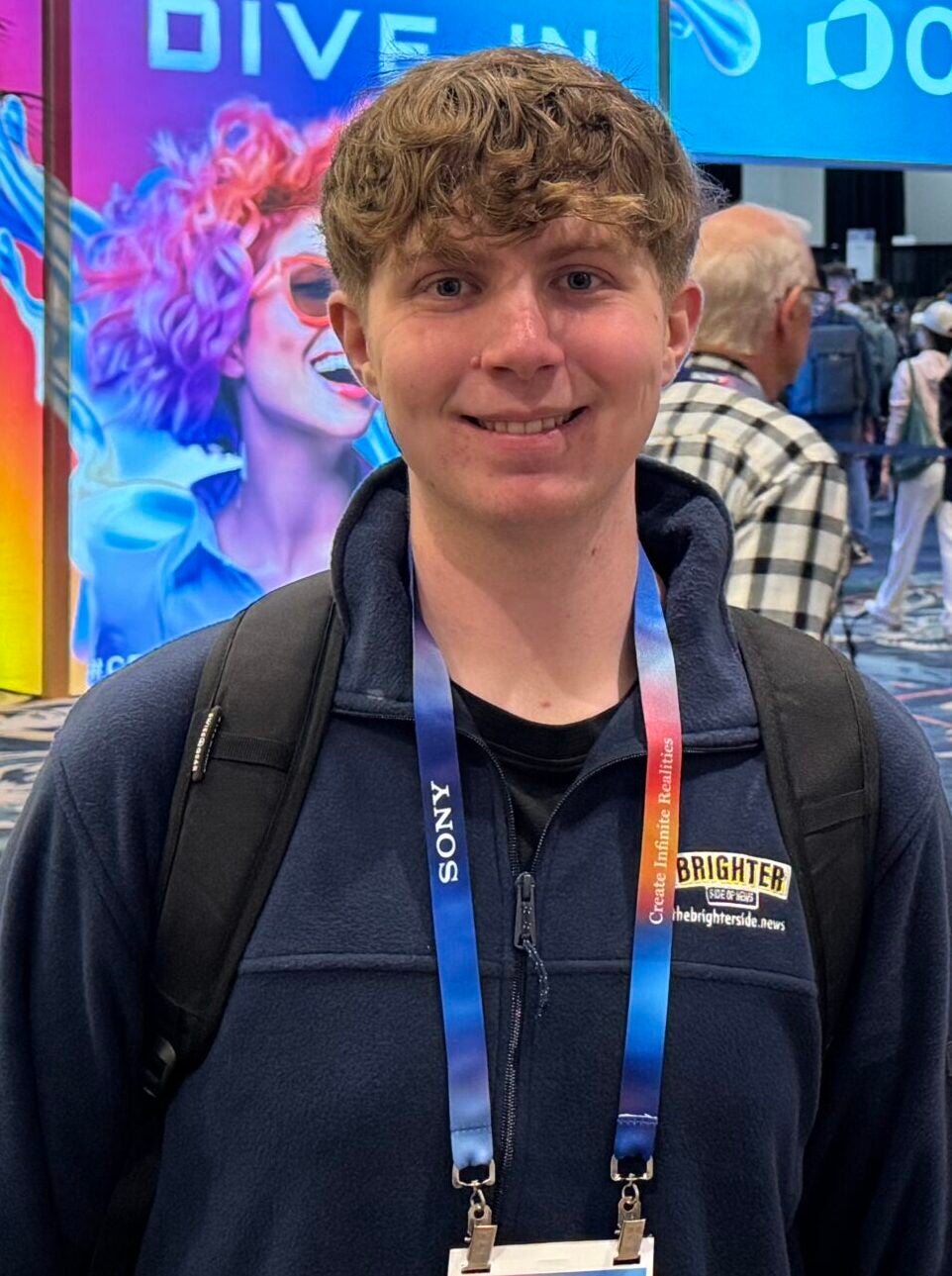
Joshua Shavit
Science & Technology Writer | AI and Robotics Reporter
Joshua Shavit is a Los Angeles-based science and technology writer with a passion for exploring the breakthroughs shaping the future. As a contributor to The Brighter Side of News, he focuses on positive and transformative advancements in AI, technology, physics, engineering, robotics and space science. Joshua is currently working towards a Bachelor of Science in Business Administration at the University of California, Berkeley. He combines his academic background with a talent for storytelling, making complex scientific discoveries engaging and accessible. His work highlights the innovators behind the ideas, bringing readers closer to the people driving progress.