Coral-inspired technology turns atmospheric CO₂ into durable, fireproof building materials
Coral-inspired technology transforms CO₂ into strong, fireproof materials, offering a revolutionary solution for carbon-negative construction.
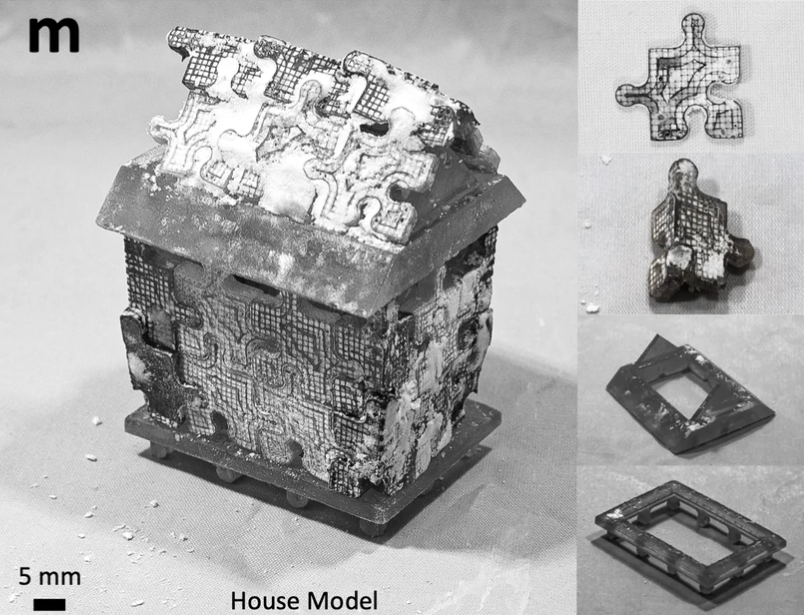
Inspired by coral reefs, a breakthrough technology captures atmospheric CO₂, converting it into strong, fire-resistant building materials for sustainable construction. (CREDIT: npj advanced manufacturing)
Carbon dioxide (CO₂), the greenhouse gas fueling climate change, is increasingly shaping our lives. It drives rising seas, fierce storms, invasive pests, and raging wildfires. Traditional approaches to controlling this gas usually focus on storing it underground or converting it into liquids. While helpful, these methods can be costly and inefficient. Now, a breakthrough inspired by coral reefs offers a better way: turning CO₂ into strong, fireproof building materials.
Researchers have developed a method modeled after how coral reefs naturally build their sturdy skeletons. Coral reefs are unique because they capture atmospheric CO₂, transforming it into solid structures with impressive strength. Scientists replicated this natural process using advanced 3D printing and electrochemistry. The outcome? A strong mineral-polymer composite with exceptional mechanical and fire-resistant properties.
How Coral Reefs Inspire Science
Coral reefs withstand extreme ocean conditions—powerful currents, predators, and erosion. Their secret lies in a process called biomineralization. Coral absorbs CO₂ from the air using photosynthesis, mixes it with calcium ions from seawater, and forms strong calcium carbonate minerals.
These minerals create a robust skeletal structure called corallites, composed of alternating layers of minerals and organic material. The structure is tough and resilient, with remarkable strength that engineers dream of copying.
Inspired by coral’s natural process, researchers created synthetic corallites using 3D printing technology. They first printed polymer scaffolds that mimic coral’s natural templates, then coated them with a thin conductive layer. These scaffolds were placed into an electrochemical circuit, submerged in a calcium chloride solution, and exposed to CO₂.
Electricity drove reactions turning dissolved CO₂ into bicarbonate ions, which reacted with calcium ions to form calcium carbonate. This mineral gradually filled the scaffold’s pores, solidifying into a sturdy composite resembling natural coral.
“This is a pivotal step in the evolution of converting carbon dioxide,” said Qiming Wang, associate professor of civil and environmental engineering at USC. “Unlike traditional carbon capture technologies that focus on storing carbon dioxide or converting it into liquid substances, we found this new electrochemical manufacturing process converts the chemical compound into calcium carbonate minerals in 3D-printed polymer scaffolds.”
Related Stories
Turning a Greenhouse Gas into Strength
The resulting composite material isn’t just environmentally friendly—it’s exceptionally strong. Tests showed these mineral-polymer composites resist shear forces as effectively as advanced engineering composites and ceramics. The structure is also highly customizable. Engineers can design precise shapes and features, adapting the materials to specific applications, from building supports to infrastructure components.
Another advantage is the composite’s remarkable ability to repair itself. If cracks form, a simple electric current can trigger chemical reactions that reconnect the broken sections. This electrochemical "healing" process restores the original mechanical strength, adding longevity to structures made from the composite.
Perhaps the most surprising quality of this composite is its fire resistance. Although the original polymer scaffold isn’t naturally fireproof, once mineralized, the material withstands direct flame exposure. In laboratory tests, composites resisted flames for over 30 minutes without structural damage.
Wang explained the unusual result: "When exposed to high temperatures, the calcium carbonate minerals release small amounts of carbon dioxide that appear to have a fire-quenching effect. This built-in safety feature provides significant advantages for construction and engineering applications where fire resistance is critical."
A Carbon-Negative Solution for Construction
Unlike traditional materials that produce carbon emissions during manufacturing, these mineral-polymer composites actively remove CO₂ from the air. Scientists conducted rigorous life-cycle assessments to measure the full environmental impact. They discovered the manufacturing process captures more CO₂ than it produces, leading to a negative carbon footprint. This means each structure built from this composite contributes positively to fighting climate change.
“With building materials and construction responsible for around 11% of global carbon emissions, our new method lays the groundwork for carbon-negative buildings,” Wang said. Such technology holds great potential for reducing the environmental impact of cities, infrastructures, and construction globally.
Additionally, the modular design allows large-scale assembly. Individual composite units can be combined into bigger structures capable of bearing heavy loads, making it feasible for major construction projects. These composites are not only environmentally sustainable but also economically viable, as they reduce reliance on energy-intensive materials like concrete and steel.
From the Lab to Your City
Currently, researchers aim to move this promising technology from the laboratory to commercial use. Their goal is to offer an affordable, scalable alternative to traditional building materials. Because the new method integrates carbon capture directly into the production process, costs could be significantly lower compared to current storage-based carbon sequestration techniques.
Future buildings and infrastructure projects could soon use this coral-inspired composite, creating a tangible impact on global carbon emissions. This approach isn’t just about sustainability; it’s about fundamentally changing how society views and manages carbon emissions. Instead of simply limiting harm, this technology actively reverses damage by embedding captured carbon into the built environment.
Wang emphasized the importance of inspiration drawn from nature, specifically ocean ecosystems: “The magic of ocean coral is fundamental to this breakthrough. Coral organisms naturally capture carbon dioxide and transform it into robust structures. We’ve adapted that incredible natural process into a scalable manufacturing method.”
By mimicking the powerful abilities of coral reefs, this new technique demonstrates how innovative thinking can unlock effective solutions for climate change. It presents a realistic pathway to integrate carbon capture directly into the infrastructure around us. The future could hold buildings not just neutral in carbon output but actively reducing carbon dioxide levels.
In a world facing urgent environmental challenges, such innovations are crucial. This coral-inspired carbon sequestration technology offers a hopeful glimpse of how we can build a stronger, safer, and more sustainable future—one structure at a time.
Researchers published their findings in the journal npj Advanced Manufacturing.
Note: The article above provided above by The Brighter Side of News.
Like these kind of feel good stories? Get The Brighter Side of News' newsletter.
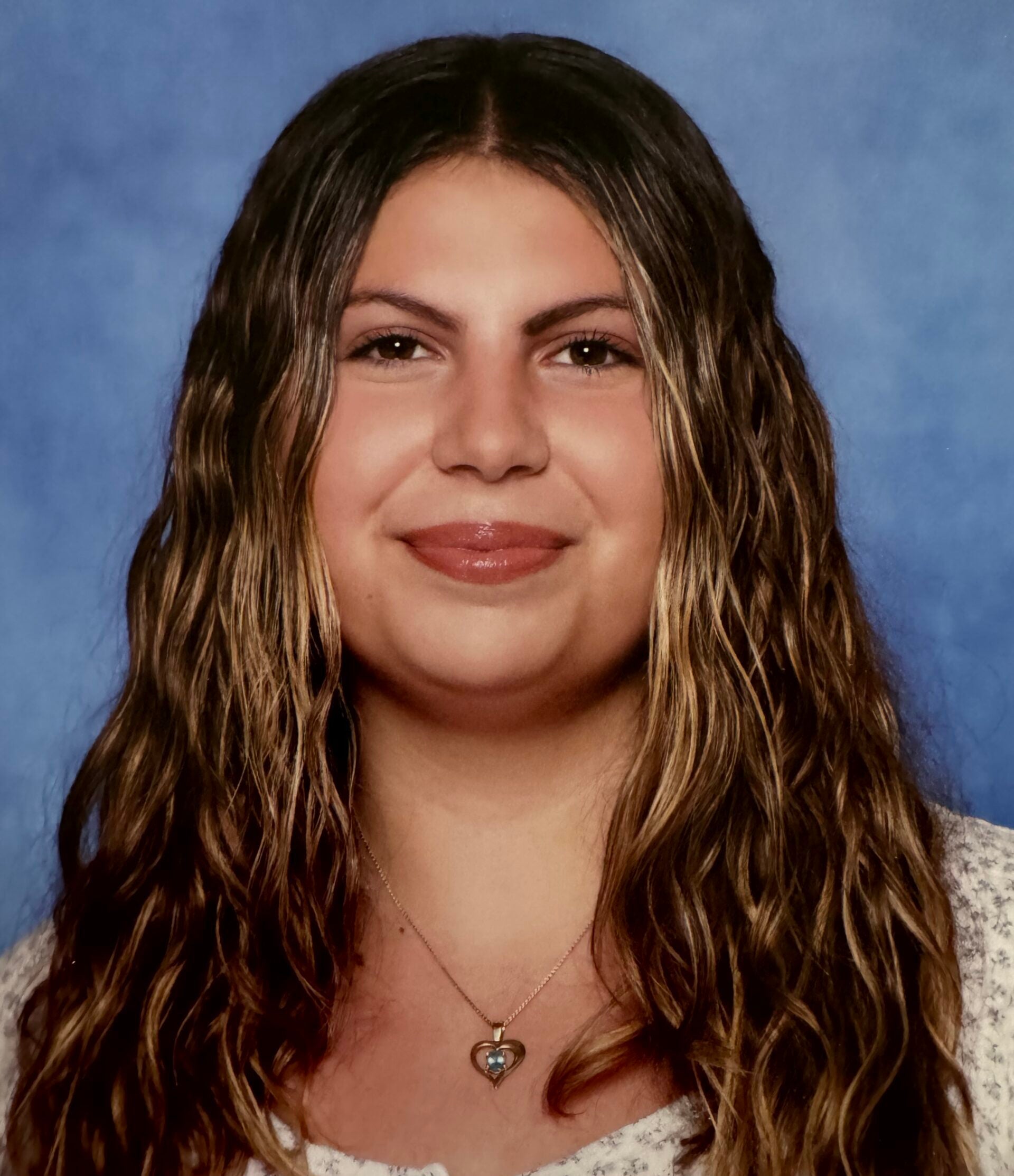
Rebecca Shavit
Science & Technology Journalist | Innovation Storyteller
Based in Los Angeles, Rebecca Shavit is a dedicated science and technology journalist who writes for The Brighter Side of News, an online publication committed to highlighting positive and transformative stories from around the world. With a passion for uncovering groundbreaking discoveries and innovations, she brings to light the scientific advancements shaping a better future. Her reporting spans a wide range of topics, from cutting-edge medical breakthroughs and artificial intelligence to green technology and space exploration. With a keen ability to translate complex concepts into engaging and accessible stories, she makes science and innovation relatable to a broad audience.