Cambridge scientists produce the world’s first zero emissions cement
Concrete, the second-most-used material in the world after water, is crucial for modern construction.
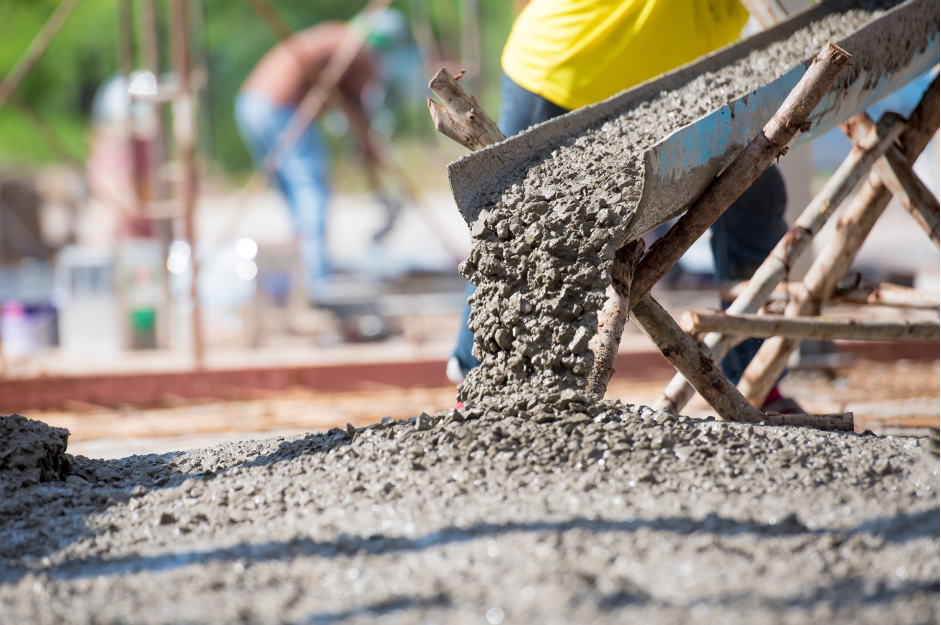
Concrete, the second-most-used material in the world after water, is crucial for modern construction. However, it's also a significant contributor to global CO₂ emissions, responsible for about 7.5% of human-caused emissions. Scientists at the University of Cambridge have now devised an innovative way to produce low-emission concrete, potentially transforming the construction industry and aiding the push towards net-zero emissions.
The breakthrough involves using electric arc furnaces (EAFs), commonly used for recycling steel, to recycle cement—the key component in concrete. This method doesn't just cut down emissions from concrete but also integrates seamlessly with existing steel recycling processes, leading to a significant reduction in the overall carbon footprint.
In conventional cement production, limestone and other materials are heated to high temperatures, releasing CO₂ in a process called clinkering. Cambridge’s new technique replaces the lime used in steel recycling with used cement, resulting in recycled cement that can be repurposed for new concrete. This approach was detailed in a study published in the journal Nature.
What's particularly promising about this method is its scalability and cost-effectiveness. Professor Julian Allwood, who led the research, highlights that the method doesn't add significant costs to the production of concrete or steel.
Moreover, tests by the Materials Processing Institute, a project partner, confirmed that recycled cement can be mass-produced using EAFs. The ultimate goal is to achieve zero-emission cement production, especially if renewable energy powers these furnaces.
“We held a series of workshops with members of the construction industry on how we could reduce emissions from the sector,” said Professor Allwood from Cambridge’s Department of Engineering. “Lots of great ideas came out of those discussions, but one thing they couldn’t or wouldn’t consider was a world without cement.”
Related Stories:
The Importance of Cement in Concrete
Concrete is composed of sand, gravel, water, and cement. Although cement constitutes only a small portion of concrete by volume, it accounts for nearly 90% of its emissions. The production process involves heating limestone to about 1,450°C, which releases substantial amounts of CO₂.
Over the years, researchers have explored alternatives to cement. Substitutes like fly ash can replace about half of the cement in concrete, but they require activation by the remaining cement to harden. Despite these alternatives, the global demand for cement—approximately four billion tonnes annually—cannot be met by these substitutes alone.
Thinking Outside the Box
“I had a vague idea from previous work that if it were possible to crush old concrete, taking out the sand and stones, heating the cement would remove the water, and then it would form clinker again,” explained Dr. Cyrille Dunant, the study's first author. “A bath of liquid metal would help this chemical reaction along, and an electric arc furnace, used to recycle steel, felt like a strong possibility. We had to try.”
The clinkering process depends on heat and specific oxides present in used cement. The researchers experimented with slags created from demolition waste, adding lime, alumina, and silica, then processed them in the EAF with molten steel. The result was a high-quality steelmaking slag and reactivated cement, achieved without adding costs to steel production.
“We found the combination of cement clinker and iron oxide is an excellent steelmaking slag because it foams and it flows well,” said Dunant. “And if you get the balance right and cool the slag quickly enough, you end up with reactivated cement, without adding any cost to the steelmaking process.”
Moving Towards Large-Scale Production
The Cambridge Electric Cement process is advancing quickly. Researchers estimate that by 2050, they could produce around one billion tonnes of recycled cement annually, roughly a quarter of the current global production. Although this recycled cement contains more iron oxide than traditional cement, it performs similarly in most applications.
“Producing zero emissions cement is an absolute miracle, but we’ve also got to reduce the amount of cement and concrete we use,” noted Allwood. “Concrete is cheap, strong and can be made almost anywhere, but we just use far too much of it. We could dramatically reduce the amount of concrete we use without any reduction in safety, but there needs to be political will to make that happen.”
A Step Towards Broader Innovation
This development not only represents a significant advance for the construction industry but also underscores the potential for innovation in reducing emissions beyond the energy sector. The researchers hope that their work will prompt greater recognition and support from governments for similar initiatives.
The team has filed a patent for their process to facilitate its commercial application. Their research received backing from Innovate UK and the Engineering and Physical Sciences Research Council (EPSRC), part of UK Research and Innovation (UKRI).
This approach, which cleverly integrates cement recycling into existing steel recycling processes, offers a scalable and cost-effective solution to one of the construction industry’s biggest challenges. As the world continues to seek sustainable solutions, advancements like these are crucial steps forward.
For more science news stories check out our New Innovations section at The Brighter Side of News.
Note: Materials provided above by The Brighter Side of News. Content may be edited for style and length.
Like these kind of feel good stories? Get the Brighter Side of News' newsletter.
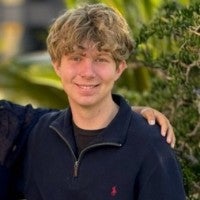
Joshua Shavit
Science & Technology Writer | AI and Robotics Reporter
Joshua Shavit is a Los Angeles-based science and technology writer with a passion for exploring the breakthroughs shaping the future. As a contributor to The Brighter Side of News, he focuses on positive and transformative advancements in AI, technology, physics, engineering, robotics and space science. Joshua is currently working towards a Bachelor of Science in Business Administration at the University of California, Berkeley. He combines his academic background with a talent for storytelling, making complex scientific discoveries engaging and accessible. His work highlights the innovators behind the ideas, bringing readers closer to the people driving progress.