3D concrete printing process captures CO2 and reduces emissions
3D concrete printing captures CO2, reduces emissions and improves concrete strength, offering a sustainable solution for construction
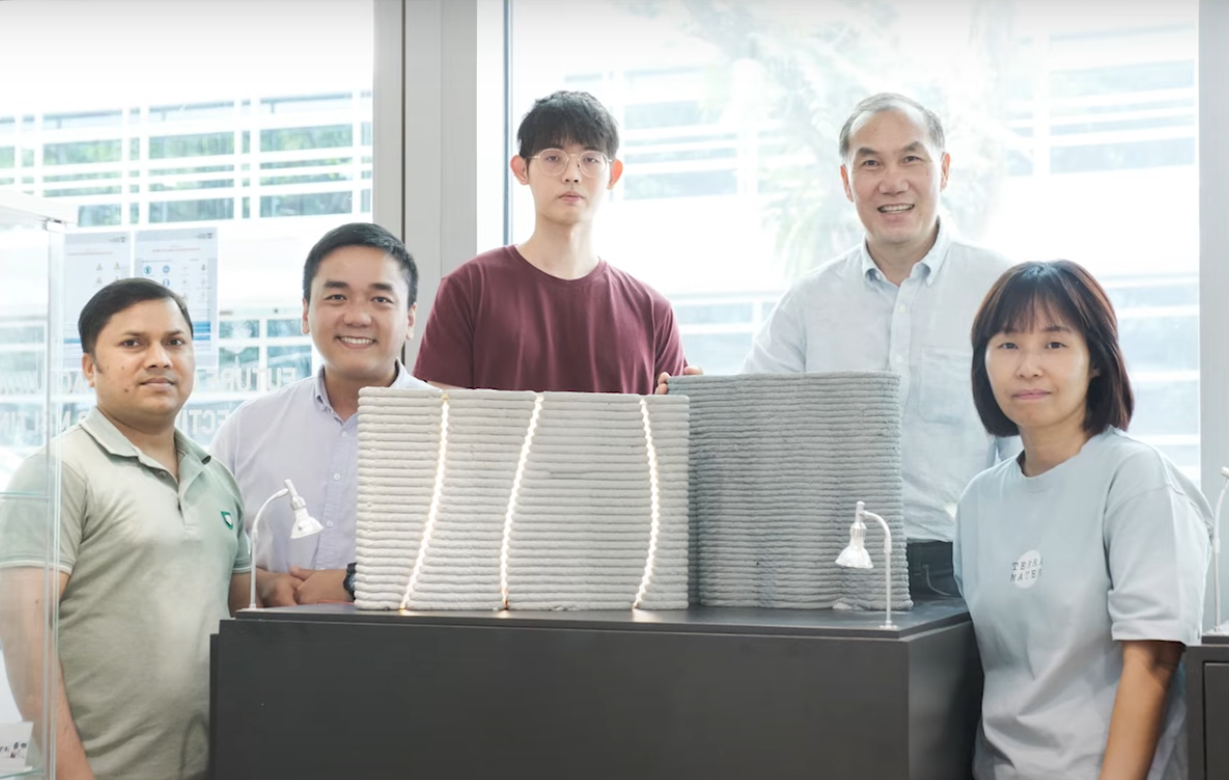
Members of the research team from the NTU School of Mechanical and Aerospace Engineering (MAE), and NTU’s Singapore Centre for 3D Printing (SC3DP), include (L-R) Dr Suvash Paul, Senior Research Fellow; Dr Daniel Tay, Research Fellow; Lim Sean Gip, PhD candidate; Prof Tan Ming Jen, Principal Investigator; Dr Lee Junghyun, Research Fellow. (CREDIT: NTU Singapore)
The building and construction sector has long driven economic progress and urban growth. However, this indispensable industry also shoulders significant responsibility for environmental challenges.
Cement production alone contributes 5% to 8% of global carbon dioxide (CO2) emissions, and construction-related activities collectively account for nearly 40% of the world’s energy-related CO2 emissions.
To put this into perspective, 54.6 billion metric tons of greenhouse gases were released into the atmosphere in 2021 alone, 14 times higher than pre-industrial levels. At this rate, the Intergovernmental Panel on Climate Change predicts global temperatures will rise 1.5°C above pre-industrial levels by as early as 2030, intensifying climate-related risks worldwide. These figures underscore an urgent need for innovative solutions that can address the construction industry’s colossal carbon footprint.
Researchers worldwide have turned to 3D concrete printing as a potential game-changer. This technology, rooted in additive manufacturing principles, promises to revolutionize construction by lowering resource use, improving efficiency, and reducing labor risks.
The technique eliminates the need for formwork, shortens supply chains, and enhances construction safety by automating high-risk tasks. It has also been estimated that 3D concrete printing could cut global energy use by up to 5%, making it as environmentally beneficial as it is practical.
The annual consumption of concrete already exceeds 30 billion metric tons globally, and demand is only rising. That’s why researchers have explored ways to merge 3D printing with carbon capture techniques—a process that can sequester CO2 directly within concrete.
In doing so, this technology offers a dual benefit: strengthening concrete while locking away harmful emissions. But how does this work in practice, and can it scale to meet global needs?
Carbon Capture and 3D Concrete Printing
Scientists at Nanyang Technological University, Singapore (NTU Singapore) have developed a breakthrough 3D concrete printing method that captures and stores CO2 within the material itself.
Related Stories
The innovation, detailed in Carbon Capture Science & Technology, reduces cement’s carbon footprint by incorporating captured CO2 into the concrete mix during printing. This approach not only traps CO2 but also enhances the mechanical properties of the final structure.
Professor Tan Ming Jen, the project’s lead investigator, explains: “The building and construction sector causes a significant portion of global greenhouse gas emissions. Our newly developed 3D concrete printing system offers a carbon-reducing alternative by not only improving the mechanical properties of concrete but also contributing to reducing the sector’s environmental impact.”
The process involves injecting CO2 and steam—byproducts of industrial processes—into the concrete mix as the structure is being printed.
The CO2 chemically reacts with calcium-based components in the concrete, forming stable calcium carbonate (CaCO3) particles that remain locked within the material. Steam enhances this absorption process, allowing more CO2 to be sequestered while simultaneously improving the structure’s strength.
Measurable Benefits
Lab tests have demonstrated the system’s remarkable benefits. The printed concrete structure showed a 50% improvement in printability, meaning it could be shaped more efficiently during construction. In terms of strength, the concrete was up to 36.8% stronger under compression—how much weight it can bear—and 45.3% stronger in bending—how much it can flex before breaking.
The method also traps 38% more CO2 compared to traditional 3D printing approaches. As a result, the technology provides a greener alternative that actively reduces the industry’s carbon footprint while maintaining superior performance.
Lim Sean Gip, a PhD candidate at NTU and the study’s first author, emphasized the innovation’s significance: “We are at a critical time where the world is accelerating efforts to meet climate change targets. We believe our technology could contribute to making the construction industry more sustainable.”
The current methods of carbon capture and storage (CCS) are often limited by high costs, scalability issues, and energy-intensive curing processes. Traditional approaches require CO2 to be stored in confined chambers, which can compromise the benefits of scalable, automated, and on-site construction.
This new 3D printing system overcomes those barriers. By integrating CO2 directly into the printing process, researchers have created a scalable, energy-efficient method that improves concrete performance while reducing emissions. In essence, the process turns a waste product—industrial CO2—into a valuable resource.
Dr. Daniel Tay, a research fellow involved in the project, highlighted its broader implications: “Our proposed system shows how capturing carbon dioxide and using it in 3D concrete printing could lead to stronger, more eco-friendly buildings, advancing construction technology.”
The Science Behind Carbonation
Previous research has shown that introducing CO2 during concrete mixing can significantly improve its mechanical properties. The CO2 reacts with calcium hydroxide and calcium silicate hydrate, forming nanoscale calcium carbonate particles. This reaction enhances cement hydration, strengthens the material, and shortens setting times.
For instance, studies have reported a 15-fold increase in penetration resistance and up to 1.16% carbon uptake within 30 minutes of CO2 mixing. Accelerated carbonation processes also create a dense microstructure known as a “carbonation shell,” which improves the material’s early-age strength. However, previous methods often focused on surface-level carbonation, limiting CO2 uptake to the outer layers of the structure.
The NTU-developed method addresses these limitations by enabling deeper, more uniform CO2 integration throughout the concrete. This advancement builds on earlier research into 3D printing for construction, which primarily focused on reducing the carbon footprint of cement-based materials through sustainable mixtures. Now, scientists are advancing the processing technologies themselves, maximizing the carbon capture potential of 3D-printed structures.
The NTU research team has filed a US patent for their innovation and plans to optimize the process further. Future developments may involve using waste gases instead of pure CO2, increasing the system’s environmental and economic efficiency. By improving the technology, researchers hope to make large-scale adoption of carbon-capturing 3D printing a reality.
This innovation represents a critical step toward sustainable construction. It offers a practical solution for reducing emissions in an industry that has long struggled to decarbonize. By turning CO2 into a valuable building resource, 3D concrete printing demonstrates the potential for greener, more resilient infrastructure.
With the global demand for concrete on the rise, this technology could help the construction sector meet its needs while staying aligned with climate goals.
As industries and governments intensify efforts to combat climate change, solutions like carbon-capturing 3D printing will be essential for achieving a more sustainable future.
Note: Materials provided above by The Brighter Side of News. Content may be edited for style and length.
Like these kind of feel good stories? Get The Brighter Side of News' newsletter.
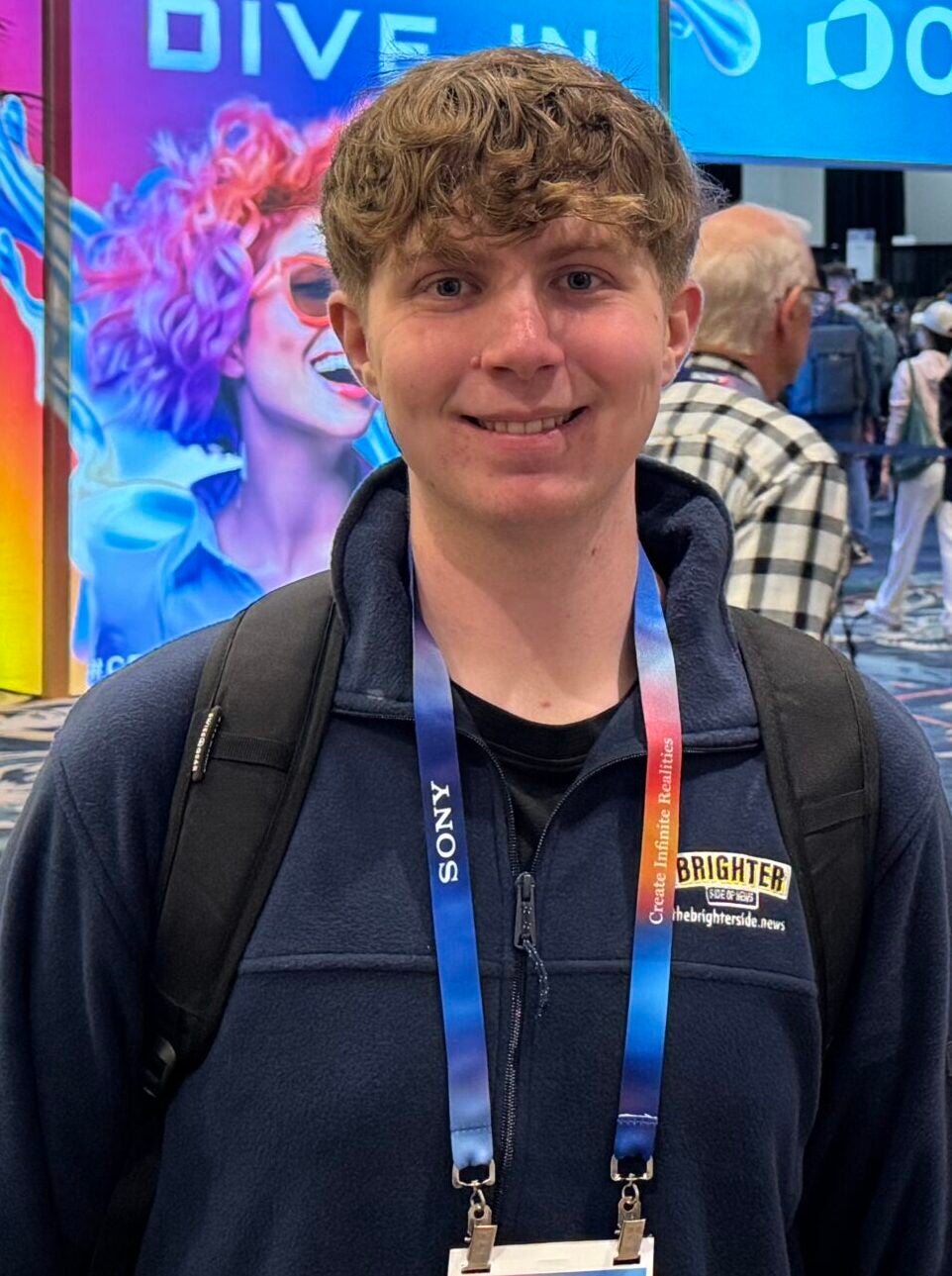
Joshua Shavit
Science & Technology Writer | AI and Robotics Reporter
Joshua Shavit is a Los Angeles-based science and technology writer with a passion for exploring the breakthroughs shaping the future. As a contributor to The Brighter Side of News, he focuses on positive and transformative advancements in AI, technology, physics, engineering, robotics and space science. Joshua is currently working towards a Bachelor of Science in Business Administration at the University of California, Berkeley. He combines his academic background with a talent for storytelling, making complex scientific discoveries engaging and accessible. His work highlights the innovators behind the ideas, bringing readers closer to the people driving progress.