Scientists develop a smarter way to recycle polyurethane
In 2022 alone, nearly 26 million tons of PUR were produced worldwide, with estimates predicting an increase to 31.3 million tons by 2030.
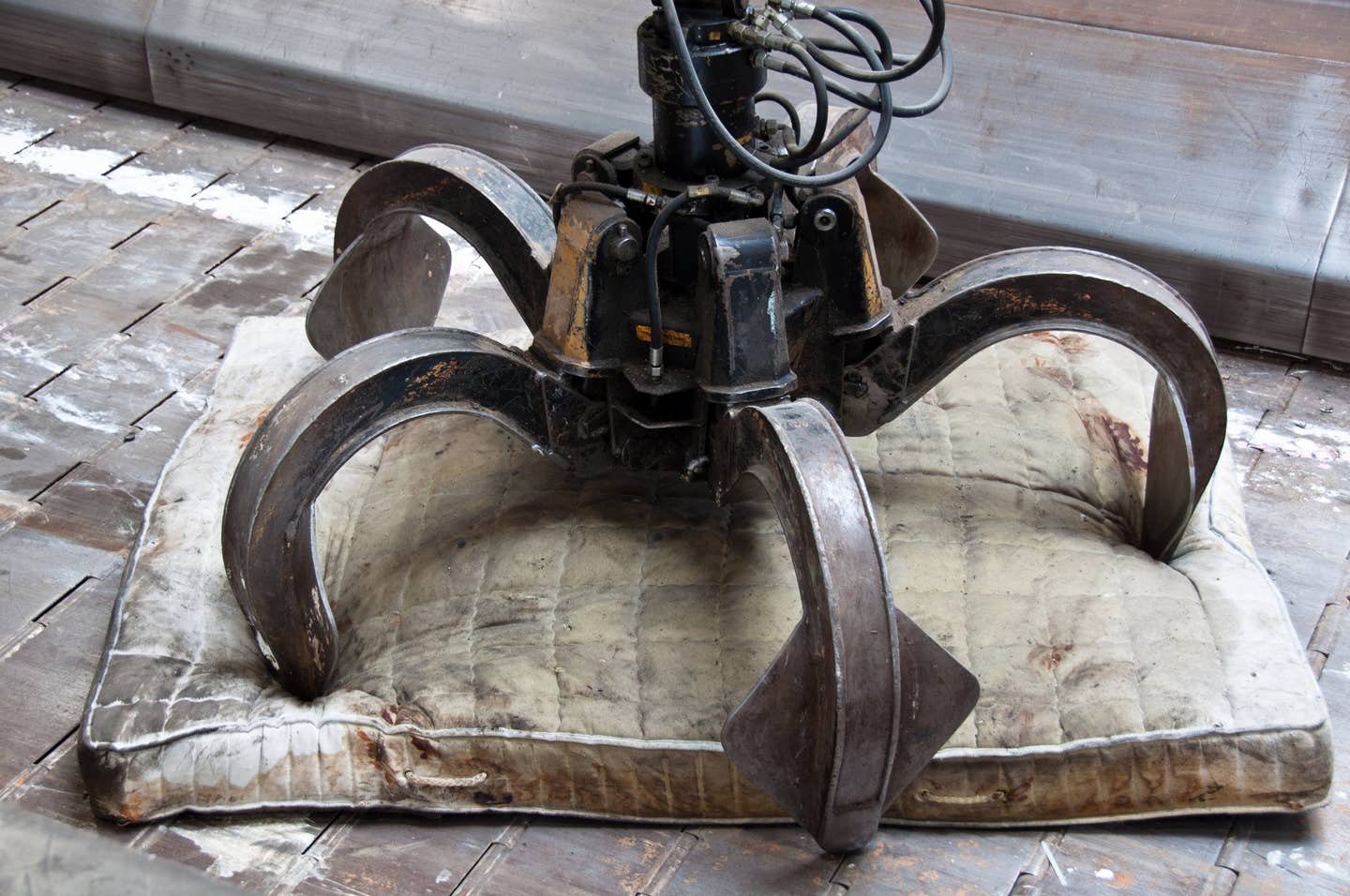
Most old foam mattresses end up in landfills or incinerators. Now, research results from Aarhus University are bringing the industry closer to being able to recycle the polyurethane foam that these mattresses are made of. (CREDIT: Colourbox)
Polyurethane (PUR) is a versatile material found in everything from mattresses and insulation to car interiors and wind turbine blades. Despite its widespread use, it poses significant environmental challenges. Most discarded PUR products are either incinerated or end up in landfills, primarily because PUR is derived from fossil oil.
In 2022 alone, nearly 26 million tons of PUR were produced worldwide, with estimates predicting an increase to 31.3 million tons by 2030. Of this, about 60% will be used in various forms of foam.
There is a growing interest in recycling PUR by breaking it down into its original components, polyol and isocyanate, through a process known as depolymerization. However, this method is not yet economically viable when compared to producing new, or “virgin,” materials. The challenge lies in the cost and complexity of separating and purifying these components after they have been broken down.
Researchers at Aarhus University have developed an innovative approach to address this challenge. Their method is based on a process already used by some companies: breaking down PUR foam using acid, a technique known as acidolysis. However, unlike the existing methods, the team from Aarhus University has succeeded in not only breaking down the PUR foam but also separating the resulting components in a single step.
This process involves heating flexible PUR foam to 220°C in a reactor with a small amount of succinic acid. A subsequent filtration step then separates the polyol, which can be directly reused in new PUR production, from the remaining solid material. This solid material is then converted into diamine through a simple hydrolysis process, which can be used to produce isocyanates, another key component of PUR.
The researchers’ method has shown impressive results, recovering up to 82% of the original material from flexible PUR foam, which is commonly used in mattresses. Their findings, published in the journal Green Chemistry, demonstrate the potential for scaling up this process.
As Steffan Kvist Kristensen, an assistant professor at Aarhus University’s Interdisciplinary Nanoscience Center (iNANO), explains, "The method is easy to scale up," making it a promising solution for recycling PUR foam waste at the production level.
Related Stories
However, turning PUR waste from consumer products into new materials will require further advancements. The PUR industry relies on specialized formulas to achieve specific properties, which adds complexity to recycling efforts. Challenges such as waste sorting, logistics, and differentiating between types of PUR must be addressed to develop a truly circular economy for polyurethane.
Beyond flexible foam, the researchers have also tested their method on other forms of PUR, including rigid foam, which is primarily used for insulation. While the technology has shown promise in these applications, significant hurdles remain.
Achieving a circular economy for PUR is still a distant goal, but the work at Aarhus University represents a significant step forward. By improving the recycling process and making it more economically viable, there is potential to significantly reduce the environmental impact of this widely used material.
The team continues to explore how the dicarboxylic acid used in the process can be reused and is testing the recycled materials in new products to demonstrate the feasibility of this recycling technology.
Note: Materials provided above by The Brighter Side of News. Content may be edited for style and length.
Like these kind of feel good stories? Get The Brighter Side of News' newsletter.
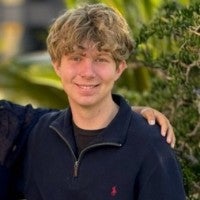
Joshua Shavit
Science & Technology Writer | AI and Robotics Reporter
Joshua Shavit is a Los Angeles-based science and technology writer with a passion for exploring the breakthroughs shaping the future. As a contributor to The Brighter Side of News, he focuses on positive and transformative advancements in AI, technology, physics, engineering, robotics and space science. Joshua is currently working towards a Bachelor of Science in Business Administration at the University of California, Berkeley. He combines his academic background with a talent for storytelling, making complex scientific discoveries engaging and accessible. His work highlights the innovators behind the ideas, bringing readers closer to the people driving progress.